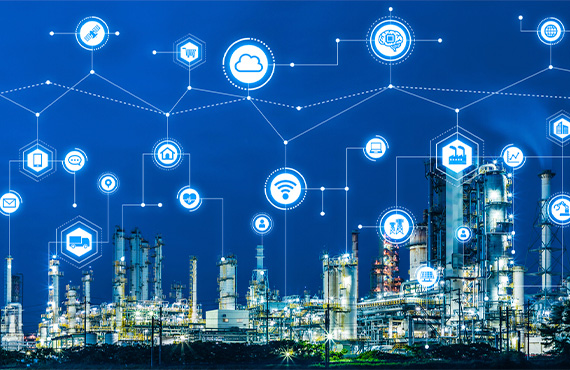
Today's crude oil refining industry is extremely competitive. Margins are tight and markets are volatile. This means that companies must be highly efficient to thrive. Small efficiency gains can have a big impact on profits. Yet, many crude oil refineries still use outdated asset management practices.
These practices limit visibility into operations and hinder efforts to improve processes. The rise of Industrial Internet of Things (IIoT) solutions provides a chance. They let us use connected assets and data analytics. They drive efficiency gains like never before. An IIoT asset management platform can bring substantial efficiency gains in crude oil refineries for their units, tanks, and across their sites.
With an IIoT asset you get real-time insights into asset health and performance. IIoT solutions let plant operators find issues faster, better plan maintenance, and fine-tune their operations. This cuts downtime and waste. In the crude oil refining industry, uptime directly links to profit. The ability to boost efficiency through IIoT asset management brings big advantages.
In this post, we will explore how IIoT asset management helps the crude oil refining process. It allows plants to operate more efficiently. We will look at the limits of traditional asset management, examine the key benefits and uses of IIoT platforms, and show how these technologies can boost productivity. They are key in crude oil refining. Refineries want to improve margins and beat the competition. To do so, plant managers must implement an IIoT asset management strategy. It is no longer just an option - it is a necessity.
Challenge with Traditional Asset Management
Traditional asset management in the crude oil refining process can be inefficient and costly. Refineries rely on big machines and complex industrial processes. Both of which are prone to unexpected downtime. Without real-time visibility into asset performance, issues can go undetected. They remain hidden until equipment fails or processes drift out of spec. This reactive approach leads to long downtime. It can cost tens of thousands of dollars per hour in lost production.
Traditional preventive maintenance programs are based on rough estimates of asset life cycles. They are not based on actual operating conditions. As a result, maintenance is done too often which costs too much. Or it's done too little which raises the risk of failure. There is limited insight into emerging performance issues or early signs of degradation.
Benefits of IIoT Asset Management
IIoT asset management provides many benefits over traditional methods in crude oil refining processes. Real-time monitoring and alerts are a key advantage. Connecting critical assets to an IIoT platform gives refineries visibility. They can see the real-time status and performance of equipment.
Measurement instrumentation sensors can monitor parameters like temperature, pressure, vibration, and flow rate. The IIoT system analyzes this data for early signs of issues. When a problem is found, it triggers alerts to maintenance teams and engineers. This allows crude oil refineries to respond immediately to avoid costly unplanned downtime. Real-time monitoring provides a proactive approach compared to traditional reactive maintenance.
Issues can be identified and addressed before causing significant disruption to operations. Old methods often don't notice problems until equipment fails or products are bad. Real-time insights allow for preventive maintenance and optimized scheduling of repairs. IIoT improves refining efficiency and uptime. It does this through early detection and rapid response.
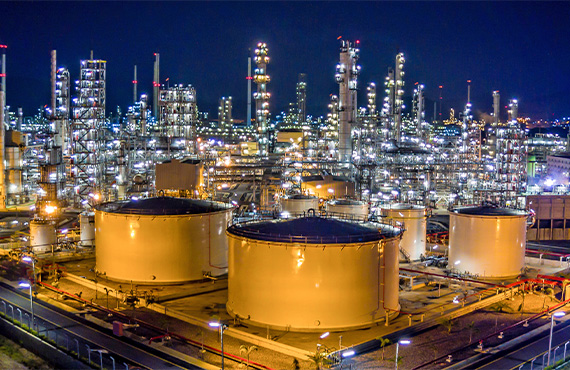
Improve Refining Efficiency
IIoT asset management allows for better efficiency in crude oil refining. It does this in a few ways:
- Reduce downtime. Use real-time monitoring and predictive analytics. They let you find potential equipment issues early and fix them proactively. This stops them from causing unplanned downtime. This avoids costly production interruptions.
- Improve issue resolution. When problems occur, IIoT asset management shows what is happening. This allows issues to be diagnosed and resolved much more rapidly.
- Improve processes by studying data on equipment and processes. This can find and fix inefficiencies. This allows for continuous optimization over time.
- Stay informed when making decisions. With all the data, managers can make better choices. They can use it for scheduling, maintenance, staffing, and more. This enhances overall efficiency.
The crude oil refining process can use IIoT to maximize uptime. It speeds repairs, optimizes continuously, and improves decision-making. This can achieve much higher efficiency. This also translates directly to bottom-line benefits.
Increase Visibility
IIoT asset management solutions provide unprecedented visibility into asset health and performance. Sensors on equipment provide continuous streams of data. They track variables like temperature, pressure, vibration, and flow rate. The data is put together and analyzed in software. It gives insights through dashboards and reports.
Managers see the status, location, and condition of assets in real time. They see them across facilities. They can spot issues as they arise. They can even predict failures before they happen based on data patterns. Operators no longer need to manually inspect equipment to check health metrics.
IIoT asset management eliminates blind spots and information gaps. It shines a light on all assets, even in remote areas. This allows for risks to be mitigated and maintenance to be better planned. IIoT has increased visibility. It now monitors assets that were previously "out of sight, out of mind" 24/7.
Optimize Maintenance
IIoT asset management allows crude oil refineries to move from reactive to predictive maintenance models. Measurement instrumentation provides real-time data on asset health and performance. They find issues early before they cause unplanned downtime.
Predictive maintenance enabled by IIoT allows maintenance to be scheduled proactively. Teams can see upcoming maintenance needs. They can plan labor and resources ahead. This prevents emergency repairs and keeps the crude oil refining process smooth.
IIoT data and analytics provide insights into failure patterns and maintenance optimization. Assets that are prone to issues can be reengineered or replaced preemptively. Maintenance schedules can be adjusted based on actual equipment performance data.
By switching from reactive to predictive approaches, crude oil refineries experience less unplanned downtime. Maintenance costs are reduced as labor and parts can be managed more efficiently. Overall equipment effectiveness is maximized across the plant.
Risk Management
IIoT asset management solutions let crude oil refineries find risks. They also stop failures before they occur. By monitoring asset health in real-time, issues can be detected early. This prevents unplanned downtime and improves overall equipment effectiveness.
Measurement instrumentation provides continuous data on vibration, temperature, pressure, and other indicators. Advanced analytics and machine learning models can detect abnormalities and alert operators. This allows for preventative maintenance and repairs before a failure happens.
With improved visibility into asset performance, crude oil refineries can better predict potential failures. Risk models identify assets that are more likely to have problems. Operators can then take action to mitigate risks. By addressing problems early, crude oil refineries avoid the high costs of unplanned downtime and repairs. Lost production time is minimized. Safety is also improved by preventing dangerous failures.
Leveraging IIoT for risk management lets crude oil refineries operate better. They can be more efficient, safe, and cost-effective. Unplanned downtime is reduced, and asset lifespan is maximized through predictive insights.
Cost Savings
IIoT asset management can significantly reduce maintenance and downtime costs in the crude oil refining process. It provides real-time monitoring and diagnostics. They let plant operators find and fix issues. This stops them from causing equipment failures or process disruptions. This preventative maintenance approach minimizes the costs. They are for emergency repairs, unplanned downtime, and lost production.
Also, the data covers asset performance and use. It can help optimize maintenance to cut labor and parts costs. Assets that are over-maintained can be identified, saving on unnecessary maintenance costs. Plant operators can flag assets for more proactive upkeep. They are under-maintained. This can stop small issues from becoming big problems. Overall, maintenance spend can be right-sized and aligned with actual asset needs.
Unplanned downtime is extremely expensive in continuous crude oil refining operations. IIoT asset management detects problems early. It also plans maintenance during outages. This avoids the significant costs of having to emergency shutdown units or processes. Production levels and yields can be maintained.
IIoT systems can use data analytics. They can also find assets and processes that are underused or inefficient. These can be optimized to reduce energy consumption and waste. Overall, IIoT asset management lets crude oil refineries increase uptime, throughput, and returns. It also cuts maintenance and operational costs.
Proconex IIoT Capabilities
Proconex offers advanced IIoT solutions for the crude oil refining industry. Our expert engineers use Emerson's top automation tech. We build strong IIoT systems to gather and study data from your critical assets.
We use Emerson's Plantweb digital ecosystem. It connects your systems. It gives you full visibility into all your operations. The AMS Device Manager gives you access to diagnostics from smart field devices. These tools help you identify issues before they cause downtime. You can also monitor the health of motors, drives, and other critical assets in real-time.
For crude oil refineries, we provide solutions to:
- Monitor asset health to schedule predictive maintenance and reduce unexpected outages
- Quickly identify abnormal conditions and take corrective actions
- Optimize energy usage and improve sustainability
- Enhance safety by proactively identifying risks
- Gain insights from analyzing operational data to improve processes
Proconex has deep expertise in crude oil refining. We can design and deploy IIoT solutions tailored to your site. Contact our experts today.
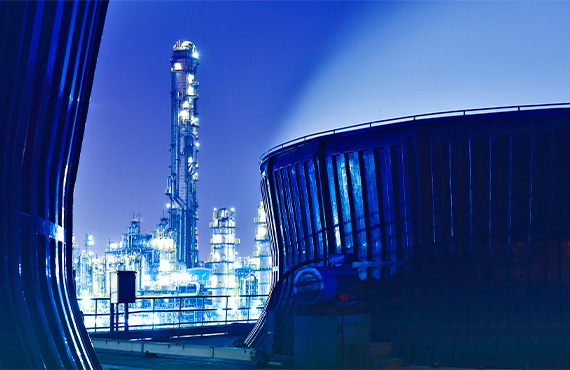
In Conclusion
Using IIoT asset management in crude oil refining has many benefits. It improves efficiency, increases visibility, optimizes maintenance, and manages risk. An IIoT solution can save refineries money. It can also help them avoid downtime and operate closer to peak performance. IIoT asset management gives crude oil refineries real-time insights into all equipment and processes. You can see all operations in one place. This lets you find and fix issues before they cause trouble. Predictive analytics enable crude oil refineries to move from reactive to proactive maintenance. Resources can be allocated more efficiently to maximize uptime.
In summary, IIoT asset management solutions give visibility and control. They are needed to drive improvement. Crude oil refineries that use these capabilities will be better positioned to meet production targets. They can also cut costs, reduce risks, and quickly adapt to market changes. The tech provides the base for higher efficiency and profit. And you can start making smart decisions with data.