
Do you feel pressure to improve productivity and efficiency in your facility? Are you constantly juggling the need for safety, compliance, and quality?
If you struggle with error-prone manual workflows, it's time to consider a game-changing solution: digitizing your process control system procedures. Imagine a world where boring paperwork and human errors are replaced. Digital workflows will streamline processes and improve performance.
First, digitizing and modernizing your maintenance procedures empowers you to significantly boost productivity while minimizing errors. No more wasted time deciphering illegible handwriting or searching through piles of paperwork. With digital workflows, you can smoothly manage maintenance tasks. You can also track progress and improve efficiency. Imagine the time and resources you'll save. This lets you focus on what truly matters: Driving your facility's success. But it doesn't end there. Going digital lets you prioritize ICS and OT cybersecurity.
You can protect data like never before. In an era where cyber threats are constant, ensuring the safety and integrity of your digital control and safety systems operations is key. Your assets and critical info are safe from potential breaches. Also, using digital maintenance workflows lets you get the most value from your assets. You can gain real-time insights and predictive analytics. They let you proactively address maintenance needs, optimize performance, and prolong equipment lifespan.
Imagine the cost savings. Imagine the operational advantages of being proactive about maintenance. In this blog post, we will look at the key benefits of digital maintenance workflows. We will guide you as you move from a paper to an automated system. It's time to unlock the power of digital workflows. They will propel your factory into a new era of success. So, if you're ready to leave manual maintenance limits, start a journey to better productivity, compliance, and efficiency. Read on.
Benefits of Digital Maintenance Workflows
By digitizing workflows, plants can dramatically improve productivity and efficiency. Technicians no longer need to search through filing cabinets. All procedures are accessible immediately on tablets and mobile devices.
Digital maintenance platforms also reduce human errors that come from manual data entry and paper-based systems. Automated workflows ensure that each step completes and documents correctly. The system identifies any missed signatures, incorrect parts ordered, and more.
With real-time data and insights, maintenance teams can optimize scheduling and staffing. The system provides visibility into upcoming preventive maintenance and service needs. Teams can then align technician schedules proactively. Digital workflows also make it easy to track the history and costs of each asset.
Industrial facilities do this by using digital control and safety systems
technologies. These solutions give their maintenance teams the tools to work smarter. Teams gain more time to focus on vital maintenance. They can do this rather than admin tasks.
Transition from Manual Processes
The shift from paper to digital workflows can seem daunting. Many plants still rely on paper-based procedures and tribal knowledge. Employees are used to doing things in specific ways. They may be hesitant to adopt new technologies and workflows.
Paper processes have many downsides. Binders can be difficult to update and track changes. Following paper checklists leaves room for human error. Finding the right document can waste valuable time during critical operations. These manual processes are stuck in the past.
Getting employee buy-in is key for a successful transition. Change management takes patience and understanding. Workers need training and encouragement to adopt digital systems. Show them how new tech can make their jobs easier, not replace their expertise.
Highlight the benefits of less paper-shuffling and efficient document control. Let them know digital workflows are the future. With full staff commitment, plants can optimize maintenance through connected, data-driven processes. The paperless path leads to greater productivity and profitability.
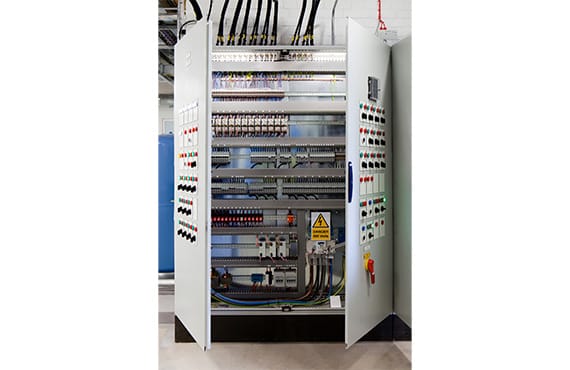
Prioritize Cybersecurity
Industrial operations rely on interconnected networks and systems to function efficiently. But more connections also make us more vulnerable. Cyber threats can seriously disrupt production. That's why prioritizing OT and ICS cybersecurity is crucial when implementing digital workflows.
Data security should be a primary concern when selecting a digital maintenance solution. Look for built-in authentication and access controls to prevent unauthorized access. Make sure to encrypt sensitive information, like equipment data or maintenance procedures. Do this for data at rest and in transit. The system should have advanced monitoring capabilities to detect potential intrusions early.
Proconex partners with industry leaders like Emerson. They provide digital maintenance platforms with built-in cybersecurity that utilize role-based access, anomaly detection, and other measures. These measures safeguard your data and operations. The right solution lets you digitize workflows. It also keeps your assets and information secure.
OT and ICS cybersecurity should not be an afterthought. It needs to be foundational when transitioning to connected maintenance systems. Prioritizing it from the start allows industrial facilities to use new tech fully. They can do this without compromising safety and reliability.
Proconex's Digital Maintenance Solutions
Proconex offers a range of industrial digital solutions to optimize maintenance workflows across industries. Our solutions integrate seamlessly with existing infrastructure to digitize paper-based processes.
We provide real-time data collection and analytics to improve productivity and reduce errors. Our easy-to-use mobile apps let technicians access procedures. They can also submit work orders and track assets from anywhere.
Proconex's digital solutions include:
- Paperless, interactive electronic work instructions accessible on mobile devices
- Digital workflows to standardize maintenance processes
- Inventory and asset management tools
- Work order management system to assign and track tasks
- Data analytics to optimize maintenance strategies
- Reporting tools to identify trends and inefficiencies
- Cloud-based platform for easy access across locations
With Proconex's digital solutions, maintenance teams can work smarter, faster, and more accurately. Technicians spend less time searching for paper manuals. They spend more time on critical tasks. Management gains visibility into operations to make data-driven decisions.
Our solutions seamlessly integrate into existing infrastructure without requiring major overhauls. We tailor our offerings to each client's specific environment and needs. Contact our experts today to learn how Proconex can change your maintenance. They do it with digital workflows.
Get Started with Digital Workflows
Transitioning from manual to digital workflows can seem daunting at first. Here are some tips on where to begin:
- Set Clear Goals and Metrics: Before making any major changes, set clear goals and metrics for what you want to achieve. This could include cutting maintenance errors by a percent. It could also mean less downtime or lower costs. Tracking metrics before and after transitioning can help measure success.
- Start Small and Build Momentum: Try implementing digital workflows for a single process or piece of equipment first. Once employees get comfortable with new digital tools, it gets easier to scale up. Starting small also allows time for training and gathering feedback.
- Prioritize Training and Communication: Make sure employees understand why going digital matters. They should know how new tools will help their jobs. Provide thorough training on any new software or processes. Digital transformation relies on people as much as technology.
- Standardize and Centralize Data: Link disparate systems together and standardize data formats. This makes data more accessible across the organization. Centralize data to analyze trends and make better decisions.
- Embrace Constant Improvement: Digital workflows require an agile, iterative approach. Seek ongoing employee feedback and continuously refine processes. What works today may need adaptation tomorrow as technology evolves.
With the right strategy, digital workflows can transform maintenance. Focus on change management and empowering employees to embrace a digital-first mindset. The benefits for productivity and efficiency are well worth the effort.
The Future of Industrial Maintenance Procedures
The future of industrial maintenance looks bright. New technologies are opening new ways to boost productivity. They let you optimize in real time. AI and machine learning have big potential. They can predict problems and spot anomalies. As systems get smarter, they can flag issues before they occur. They can also recommend ways to prevent them. This shift is from reactive to proactive maintenance. It will boost uptime and ensure assets operate well.
Digital twins and simulations are rising. You can test maintenance procedures first in a virtual environment. There, they can also refine. Augmented reality will also help with maintenance. It will give technicians step-by-step visual instructions and remote expert advice.
Technology removes the manual effort in capturing and analyzing data. This allows maintenance teams to focus on higher value tasks. Their specialized expertise will continue driving improvements in asset reliability and performance. Maintenance will become more automated. It will also have seamless data integration and intelligent systems will work with humans.
Organizations that use digital workflows and new technologies will gain a competitive advantage. Companies can confidently navigate their maintenance digital transformation with Proconex as a partner.
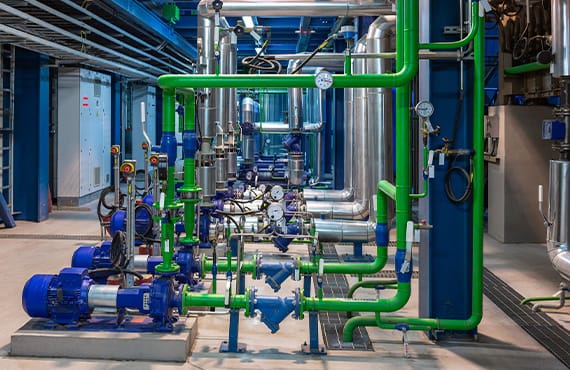
To Summarize
Moving from manual to digital maintenance workflows has many benefits. This is true for all types of industrial facilities. By boosting productivity and cutting errors. By putting cybersecurity first. Organizations can modernize their digital age maintenance procedures. Automated processes are efficient and save money. Predictive analytics and machine learning control them.
Teams can use real-time data and insights. They can detect issues early and prevent downtime. Digitization also minimizes human error while capturing invaluable data to continuously improve. However, realizing these benefits requires selecting the right digital solutions partner.
Proconex has over 75 years of experience implementing process control systems. We have the expertise to guide your digitization journey. Learn more about our Emerson partnership and full-service offerings tailored to your needs. The future of maintenance is digital - let's discuss how to get you there today.