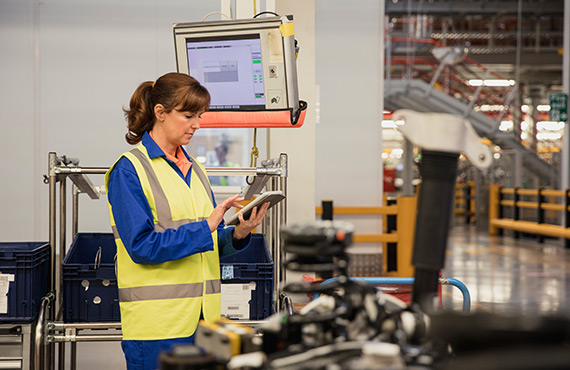
For decades, industrial facilities have relied on manual process control systems.
Yet, upgrading to modern automated control brings about significant benefits. Automating process control replaces outdated manual operations with integrated, real-time measurement. Monitoring and change are also integrated. Software and instrumentation drive the new system.
This transition from human-directed to technology-enabled operations leads to major improvements. These include efficiency, quality, safety, costs, data visibility, and more.
This article explores the limitations of sticking with manual control. It also discusses the many advantages of shifting to automated systems.
These benefits include streamlined operations and reduced errors. They also expand data collection capabilities and provide predictive insights. Industrial facilities that want to modernize can gain a powerful competitive edge. They can do this by automating process control.
Limitations of Manual Control
Manual process control systems rely on human operators. They track conditions, make adjustments, and maintain optimal settings. Yet, this hands-on approach comes with its fair share of drawbacks.
- Manual systems lack automatic feedback loops. As a result, they depend on operators' expertise and diligence. This makes them prone to human error and inconsistency. Even the most skilled operator can make mistakes or be inconsistent. This can result in variations in product quality.
- Fatigue reduces performance. After long shifts, people monitoring gauges and equipment get mentally tired. As concentration wanes, the risk of errors increases.
- Operators must test samples. They make small adjustments to account for even the slightest fluctuations. This constant hands-on need keeps personnel use high.
- Limited data collection hinders the availability of historical data. This makes it difficult to analyze trends and performance. This is because there are no automated sensors and data logging.
- It's difficult to optimize. Maintaining optimal conditions 24/7 can be challenging with manual control. There are inevitable lags as operators respond to changing requirements.
These drawbacks highlight the need for automated systems.
Improve Efficiency
Automating process control systems revolutionize operational efficiency in many significant ways:
- Automated systems can detect and correct problems within seconds or milliseconds. This lightning-fast response time is incredible. This eliminates the need for lengthy manual troubleshooting. This reduces waste and ensures tighter control over parameters.
- Automated systems provide real-time data on all process parameters. They ensure constant oversight, rather than sporadic manual checks. Any deviations can be immediately identified before they impact the final product.
- The advanced automated controls can balance different variables. These include temperature, pressure, and flow rate. This holistic approach optimizes the entire process. It doesn't focus on individual parameters.
- Automated systems operate 24/7, free from fatigue or human error. This is reliability at its finest. As a result, the output becomes more consistent. There are fewer interruptions caused by starting and stopping.
- Seamless scalability: Automated systems make it effortless to add control points. The control system can adapt as operations expand or processes evolve. It does not need extensive rework.
Transition from manual to automated process control to unlock productivity and efficiency.
Enhance Quality and Yield
With manual control systems, the product quality and process efficiency can vary.
How?
Well, it depends on the operator and their attentiveness to varying conditions.
On the other hand, an automated system monitors critical parameters. It makes real-time adjustments to optimize conditions. This results in improved product quality and yield. Automation allows for precise control over variables.
These include the following:
- Temperature
- Pressure
- Flow rates
You get enhanced consistency and reduced waste. Additionally, you can analyze detailed data histories provided by automation.
Increase Safety
By transitioning from manual to automated process control, operational safety is enhanced as it minimizes human exposure to hazardous chemicals, high temperatures, moving machinery, and other dangerous conditions on the plant floor.
Personnel don't need to take manual measurements, monitoring, or adjustments. Instead, they can manage tasks like opening and closing valves. They can also regulate pressures and start shutdown sequences with an automated control system.
With automated safety systems, plants can establish automated interlocks and shutdowns. If critical process parameters surpass acceptable limits or equipment malfunctions are detected, the system takes action. It shuts down or isolates a specific part of the process before safety risks escalate.
Reduce Labor Costs
Automated process control systems offer significant advantages over manual control. They reduce labor costs, in particular. These systems can operate without direct oversight. They perform control actions, collect data, and analyze autonomously, based on programmed parameters.
Automated systems allow manufacturers to need less direct oversight and intervention from operators. This allows the systems to run for longer periods unattended. The reduced need for operators per shift lets them take on more valuable roles.
Further, automation lowers the risks linked to human errors and inconsistencies. It provides greater repeatability and precision. It eliminates the need for operators to engage in tedious manual data collection. It also eliminates the need for operators to engage in tedious manual recordkeeping.
Automated systems also enable faster, more informed decision making. They do this by using the generated data. This eliminates the delays associated with manual processes. It allows manufacturers to make more timely and accurate decisions.
Also, automated control systems also reduce the cost of training new operators for manual processes. These systems have a consistent approach.
Implementing automated process control systems can save on labor costs. This makes it an attractive investment. Often, the system can pay for itself within a year or two from the savings in labor costs.
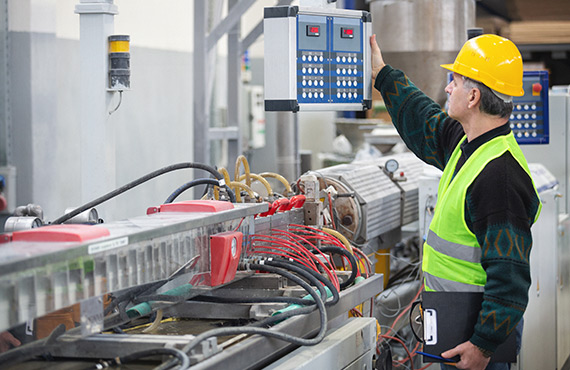
Data Collection Analysis
Upgrade to automated process control.
Why?
Well, you can gather vast amounts of real-time data on every aspect of your operations. This valuable information allows you to pinpoint any issues. It also helps you uncover opportunities for enhancement.
- Check process variables, such as temperature, pressure, and flow rate. Look for any deviations from optimal parameters. You will receive automatic alerts for critical events.
- Gather production and quality data to identify bottlenecks, waste, variability, and underperforming assets.
- Keep track of equipment effectiveness and usage. This helps optimize maintenance and make informed decisions about future capital investments.
- Analyze energy consumption metrics to discover ways to reduce costs.
- Store historical data to identify patterns and trends over time.
- Use data analytics and advanced software to transform data into actionable business intelligence.
- Share key production metrics across departments and teams. This helps to align all team members around common goals.
- Integrate data with ERP, MES, and other systems. This enables enterprise-wide visibility and smarter decision making.
Invariably, automated systems have improved data collection and analysis.
Easy Integration
Many manufacturers worry that upgrading to modern process control systems will force them to tear down and replace their entire existing infrastructure. Yet, by partnering with the right company, integrating new process control technologies can be a seamless and cost-effective process.
Proconex has over 70 years of experience. We specialize in integrating the latest solutions into brownfield sites. These sites have legacy systems and infrastructure. Our team of experts can conduct comprehensive assessments. We can determine which existing assets we can use. We can also identify areas where we can make new investments that will have the greatest impact.
Proconex partners with leading control system providers like Emerson. This ensures that our solutions are designed for interoperability. Open platform architecture and digital ecosystems have made it much easier to connect different systems today. Additionally, we offers services to handle data migration.
Proconex offers strategic guidance and technical expertise.
What does this entail?
This means you can upgrade to modern process control systems without the headaches of a complete rip-and-replace.
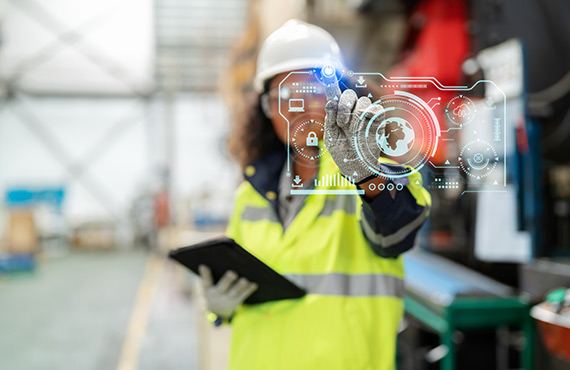
Key Takeaways
Upgrading from manual to automated process control systems offers a wide range of advantages. It can revolutionize manufacturing operations.
By adopting these advanced solutions, you can achieve:
- Enhanced efficiency through increased productivity and minimized downtime. Automation allows for optimized production 24/7.
- Improved quality and yield by minimizing human errors and variations. Automated systems ensure consistent and precise control.
- Heightened safety for personnel by reducing direct exposure to hazardous processes. Automation mitigates risks.
- Reduced labor costs by eliminating the need for round-the-clock manual supervision. Automated systems can operate without constant oversight.
- Enhanced data collection and analysis through automated logging of all process parameters. This data enables continuous optimization.
- Seamless integration with existing infrastructure thanks to flexible and modular automation systems.
Discover how Proconex can assist you in upgrading your process control systems.
We provide comprehensive solutions tailored to your specific operations and objectives. Our experienced team is ready to assess your needs.
Partner with us to bring your manufacturing operations into the modern era of automated process control.