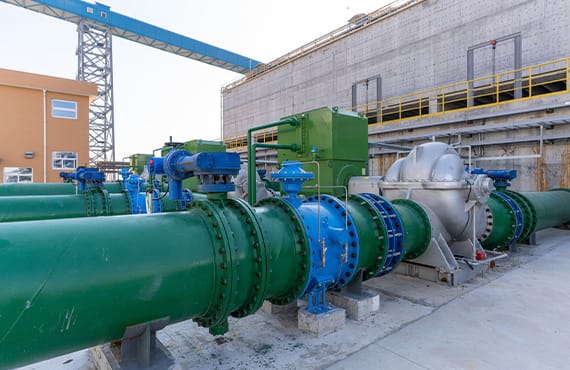
Are you in an industry that deals with hazardous materials, high temperatures, pressures, or all the above? If so, you already know the importance of ensuring safety measures are in place to protect both your employees and your valuable assets.
That's where Safety Instrumented Systems (SIS) come into play. SIS plays a crucial role in sectors such as oil, gas, and chemicals. It's also vital in power generation, metals, mining, and pharmaceuticals. They monitor key variables and parameters. They constantly scan for signs of hazards.
When limits are exceeded, SIS takes action. It closes valves, pumps, and other critical parts. This shuts down the process in a controlled way. One small mistake or problem in these areas could have catastrophic results. That's why SIS applications are crucial. They are used for emergency shutdowns on offshore platforms and for safety interlocks at nuclear plants. They also play a vital role in burner management, fire and gas monitoring, and overpressure protection on nuclear reactors.
The ability of SIS to detect abnormal conditions and act swiftly is what makes them indispensable. They keep operations safe and prevent disasters that could harm people and the environment. This is precisely why rigorous and ongoing SIS testing is essential.
Without thorough testing, how can you be sure your SIS will work perfectly when it matters? Trusting in untested or faulty systems is simply not an option. By investing in rigorous SIS testing, you are ensuring the ongoing reliability and effectiveness of your safety measures.
Whether you're responsible for an offshore platform or a nuclear plant, don't leave anything to chance. Prioritize SIS testing to protect your operations, your people, and the world around you. It's a small price to pay for peace of mind and the assurance that your safety measures are indeed up to the task. Read on to learn more about how SIS testing keeps dangers at bay.
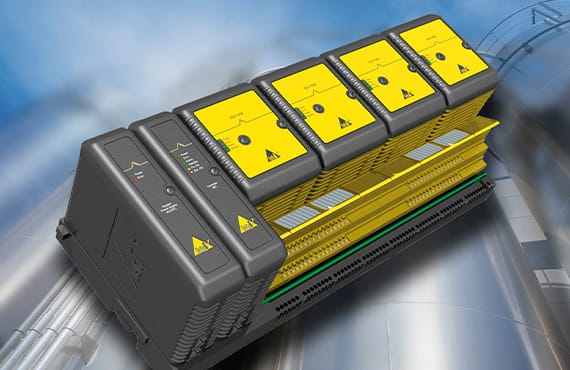
What is a Safety Instrumented System?
Safety Instrumented Systems protect people, the environment, and assets in many industrial workplace environments. They also act as the last line of defense in industrial process control systems. They take emergency action when parameters exceed safe limits.
SIS like Emerson’s DeltaV SIS™ are vital for industries like oil and gas, chemicals, power generation, metals, mining, and pharmaceuticals. In these industries, processes involve hazardous materials, high temperatures, and pressures. SIS checks key variables and parameters to detect when a hazard is developing. SIS will also close valves, pumps, and other parts if they exceed certain limits. This will shut down the process safely and reduce dangers. SIS applications include:
- Emergency shutdown on offshore oil rig platforms
- Safety interlocks at nuclear power plants
- Burner management
- Fire & gas monitoring
- Overpressure protection on nuclear reactors
Their ability to act quickly, and without manual intervention, during abnormal conditions makes SIS vital for industrial facilities. It keeps operations safe and prevents catastrophes. The safety of the facility, its workers, and its surroundings depends on SIS working right. So, we need rigorous SIS testing.
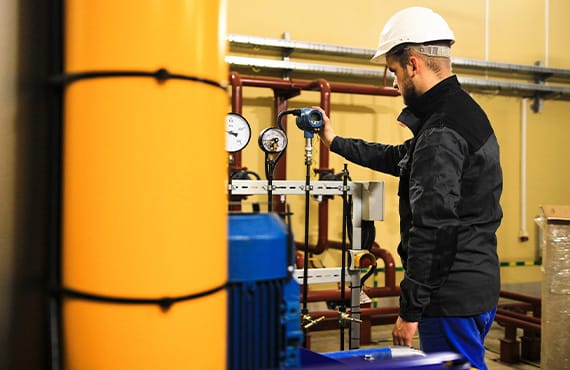
SIS Testing Types
Safety instrumented systems need rigorous and regular testing to ensure they remain effective. There are three main types of SIS testing that facilities should conduct:
- Operations Testing: Operations testing involves periodic testing of SIS during normal operations. This includes testing individual components like sensors, logic solvers, and final elements. Operations testing verifies these components are functioning per design. The procedures are typical for testing operations. They include bump tests, channel checks, and partial valve testing. Performing regular operations testing helps confirm safety system performance over time.
- Maintenance Testing: Maintenance testing is more thorough. Taking safety functions out of service does it. This allows thorough inspection without interrupting production. Maintenance testing examines the full SIS chain. Typical procedures include calibrating sensors. They also include diagnosing controllers and testing I/O. They also test valves across their full stroke. Performing rigorous maintenance testing is crucial for keeping SIS health optimal.
- Turnaround and Shutdown Testing: The most exhaustive SIS testing happens during scheduled turnarounds and shutdowns. This allows access to all safety instrumented functions for complete verification. Turnaround testing often includes physical inspection, reconfiguration, and replacements. Shutdown testing provides the opportunity to perform full stroke testing on final elements. Conducting intensive turnaround and shutdown testing ensures SIS integrity for future operations.
Regularly performing all three testing types is critical for reliable SIS performance. The ongoing tasks are operations, maintenance, and turnaround testing. They provide assurance that safety systems will work when needed.
SIS Testing and Cybersecurity
SIS systems are vulnerable to cyber threats. These can risk operations and personnel's safety. Regular testing is key. It finds weaknesses that bad actors could exploit. SIS is now more connected than ever. These systems are at risk of cyber-attacks. These attacks aim to hurt safety and cause disruptions. Hackers can access and change sensor readings. They can also alter setpoints or disable alarms. This can lead to dangerous situations. Safety interlocks fail to activate when they should because critical thresholds are exceeded.
Real-world examples demonstrate the need for diligent SIS testing and cybersecurity:
- In 2021, a ransomware attack shut down the Colonial Pipeline in the US, halting fuel delivery for days. Safety systems could suffer similar compromises.
- The TRITON malware was designed to disable Triconex safety instrumented systems, and was responsible for shutting down a petrochemical plant in Saudi Arabia in 2017.
- Stuxnet specifically targeted Siemens S7 SIS equipment in uranium enrichment facilities in Iran, reprogramming PLCs to override safe operating parameters.
Regular and rigorous testing regimes by knowledgeable partners like Proconex are essential. SIS testing can find communication gaps and application errors. It can find hidden malware or unauthorized changes before safety is compromised. Maintaining robust cybersecurity and performing frequent testing ensures reliable SIS protection.
Digital Workflows for Testing
Digital workflows are changing SIS testing. They do this by boosting efficiency, improving compliance, and enabling data insights. Digitizing paper-based processes gives companies real-time visibility into testing status. It also reduces the risk of human error.
Digital solutions like electronic workflows and digital reporting provide the following key benefits:
- Automated notifications and prompts ensure tests are completed on schedule and results are properly documented. This improves compliance with safety regulations.
- Centralized data gives managers an integrated view of testing KPIs across all sites. This enables data-driven maintenance strategies.
- Electronic forms with validation replace manual data entry, reducing transposition mistakes.
- Instant access to historical test records makes audit preparation easier.
- Electronic archiving of test results cuts document storage needs.
Digital workflows are streamlined. So, reliability engineers can focus less on paperwork and more on safety strategy.
Proconex offers digital solutions. We provide clients with better efficiency and compliance. By using Proconex's digital abilities, you can get more from your SIS testing programs.
The Value of Regular SIS Testing
Regular SIS testing has immense value. It reduces risks and ensures the ongoing integrity of your safety systems. Testing requires time and resources. But the long-term benefits make it worth it.
Testing frequently allows you to identify issues before they cause major problems. Fixing even small glitches improves reliability. It also prevents dangerous failures later. Routine testing has small costs. However, they prevent much larger expenses from disruptions, fines, and, worst of all, safety incidents.
Many industrial regulations mandate proof of periodic SIS testing. This includes standards like IEC 61508/61511 for the process industries. Skipping tests puts you out of compliance. Violations are costly. So are the repercussions from lapsed safety systems. They cost more than the testing.
Ultimately, regularly verifying your SIS performance provides peace of mind. You can rest assured your critical safeguards are functioning as intended. The benefits of ongoing testing include: less risk, no downtime, ensured compliance, and, most importantly, better protection for your people, assets, and community.
Working with experts like Proconex adds even more value. It maximizes your SIS testing investment.
Best Practices for SIS Testing
To implement an effective SIS testing program, you must follow best practices. You must also optimize your approach.
Here are some of our key recommendations:
- Develop a detailed testing checklist covering all critical tests and procedures. Having a comprehensive checklist ensures you don't miss any key tests.
- Schedule testing based on a risk-based methodology. Test the most critical SIS components first. They are the most prone to failure.
- Involve both maintenance technicians and engineers in testing. Technicians provide hands-on expertise while engineers ensure proper test procedures.
- Perform testing across operational states including standby, running, shutdowns, and startups. Testing in different states reveals issues that may not appear otherwise.
- Validate test equipment and software before use. Confirm tools are properly calibrated and configured for your systems.
- Retain detailed testing records and documentation. Maintain evidence of testing activities for audits and regulatory compliance.
- Analyze test results to identify areas for improvement. Look for common failure points or deficiencies to address.
- Get management buy-in for time and resources. Demonstrate how proper testing reduces risks and costs in the long run.
- Continually optimize your testing program based on results. Adjust frequencies, scope and procedures to maximize effectiveness.
Following SIS testing best practices gives you confidence that your safety systems will work when needed. Partnering with testing experts like Proconex can help. We can implement a program tailored to your facility's needs.
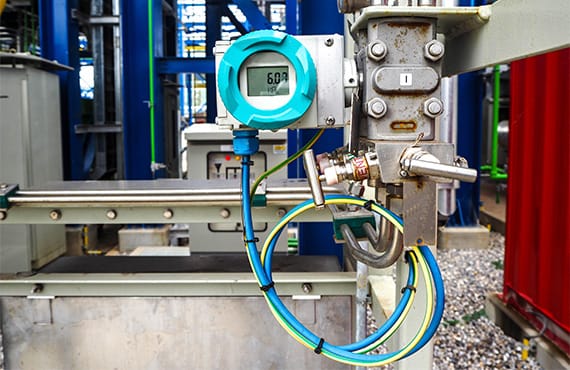
Regular SIS Testing is Essential
As we've discussed, SIS testing has a few main forms. These are: Operations testing, maintenance testing, and turnaround/shutdown testing. Implementing structured testing procedures and digital workflows can optimize these processes. Partner with an experienced SIS testing provider like Proconex. This ensures you use industry best practices. Our experts bring decades of hands-on domain knowledge across your industry.
We stay on top of the latest safety regulations and cybersecurity threats. Trust us to validate your safety systems, identify any issues, and recommend solutions. Don't cut corners on SIS testing.Doing so puts your operations, finances, and personnel at risk. Prioritize regular, rigorous testing to protect your people, community, and environment.
Contact Proconex today to learn more about our SIS testing and cybersecurity services. Together, we can build robust defenses to keep your operations safe.