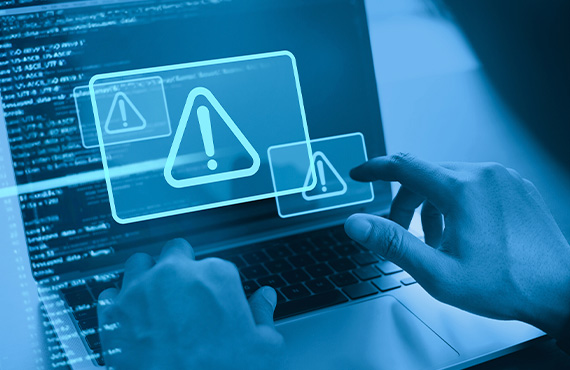
Industrial control systems (ICS), like the ones we provide here at Proconex, are vital to running modern industrial operations and infrastructure. The systems include supervisory control and data acquisition (SCADA) systems.
They also include distributed control systems (DCS) and other control system setups. These setups include skid-mounted Programmable Logic Controllers (PLCs). They're common in industrial sectors and critical infrastructure.
ICS are used to control and monitor physical processes. These processes generate and send electricity. They also manage water, oil, and gas pipelines. They manage chemical plants, transportation, and manufacturing. They provide automation, visibility, and control for operations. ICS are also used for remote monitoring, integration, and data sharing. This exposes them to cybersecurity risks. A cyber attack could cause loss of control and dangerous real-world impacts.
Securing ICS against cyber threats has become a priority. Asset owners across critical infrastructure now make this a primary focus.
Common Cyber Threats Facing Industrial Control Systems
Some of the most common threats to ICS include:
- Malware, ransomware, and phishing attacks: Malicious code and phishing emails are prevalent methods for infiltrating ICS networks. Ransomware can lock down control systems until a ransom is paid. Targeted phishing emails trick users into downloading malware or sharing login credentials. These attacks can spread quickly between IT and OT systems.
- Insider threats: Disgruntled or careless employees are a top source of security incidents. They may intentionally access unauthorized data or inadvertently expose vulnerabilities in the ICS. Strict access controls and monitoring employee actions can help mitigate insider risks.
- Supply chain compromises: The expanding digital supply chain provides new surfaces for attackers to exploit. Someone could use compromised hardware, software, or third-party credentials to breach the ICS environment. Vetting suppliers and limiting integration points reduces exposure.
- Unauthorized access: External threat actors frequently scan for open ports, unpatched systems, and other vulnerabilities to break into ICS networks. Once inside, they may shut down processes, modify data, or cause physical damage. Network segmentation, multi-factor authentication, and proactive monitoring all help thwart unauthorized access attempts.
Vulnerability in ICS
Many of these vulnerabilities stem from the nature and purpose of ICS.
- Legacy systems: ICS often rely on legacy hardware and software that were designed years ago, long before cybersecurity was a major concern. They lack modern security features and protocols.
- Lack of security features: ICS focuses on reliability and performance, not security. They don't have traditional IT security tools like antivirus software or firewalls. Authentication controls and encryption are often absent.
- Poor segmentation: ICS networks are often flat with no segmentation between critical control systems and business networks. This provides attackers an easy pathway to access core ICS components.
- Weak authentication: Default passwords and credentials are often left unchanged in ICS environments. Multi-factor authentication is rarely implemented, enabling attackers to easily guess passwords.
- Unpatched systems: ICS utilize specialized hardware and software that can be difficult to update. Patches may disrupt delicate processes. As a result, ICS systems often remain unpatched for vulnerabilities.
These factors create security gaps. Attackers can exploit them to gain access. They can steal data, disrupt operations, or cause damage.
Addressing these vulnerabilities is key to securing modern ICS environments against cyber threats.
Real-World Attacks on Industrial Control Systems
Major cyber attacks have targeted industrial control systems (ICS) in recent years. They show the real dangers ICS face.
Some notable examples include:
- Stuxnet: Discovered in 2010, Stuxnet was a sophisticated worm designed to target programmable logic controllers used in Iranian nuclear facilities. It caused substantial damage by manipulating control systems and sabotaging centrifuges. Stuxnet took advantage of multiple zero-day vulnerabilities and showed how an advanced cyber weapon could impact physical infrastructure.
- TRITON: Also known as Trisis, TRITON was malware discovered in 2017 that targeted Triconex safety instrumented systems. These are designed to safely shut down industrial processes when dangerous conditions occur. TRITON could reprogram the devices to fail unsafely. This could cause physical damage. It impacted an organization in the Middle East.
- Ukraine Power Grid: In 2015 and 2016, hackers were able to gain remote access to Ukraine's power grid and trigger blackouts, impacting hundreds of thousands of people. They were able to override operator commands and open circuit breakers, leveraging insider knowledge of the systems. This demonstrated threats to critical infrastructure like electric utilities.
- Colonial Pipeline: A 2021 ransomware attack on this major US fuel pipeline operator disrupted gasoline delivery for days. The attackers exploited poor cybersecurity practices to infiltrate IT systems and encrypt files. Though not directly targeting ICS, it's shown interdependencies between IT and OT systems.
These incidents reveal real-world cyber risks facing industrial facilities. Attackers can and want to disrupt critical infrastructure. They aim to do so for sabotage or profit.
It’s crucial to take threats seriously and apply robust ICS cybersecurity measures.
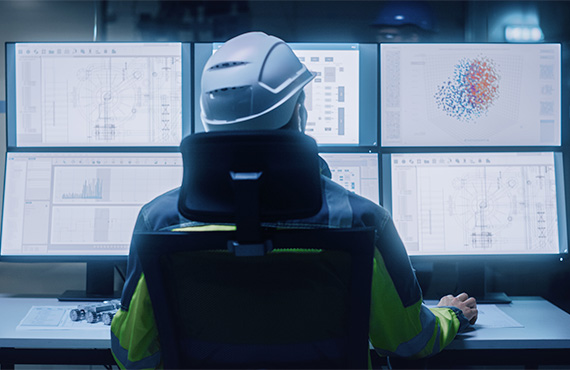
Impact of Cyber Attacks
Cyber attacks on industrial control systems can have severe consequences, including:
- Production downtime: A successful breach that disrupts ICS operations often results in extended downtime and lost productivity. Malware infections, network outages, or manipulated processes can shut down production. It can be for hours, days, or even weeks. This leads to big financial losses. It also makes customers unhappy and harms the company's reputation.
- Environmental hazards: Manipulating chemical processing, energy generation, or other industrial operations can directly cause environmental incidents, such as chemical spills, gas leaks, or explosions. Cybercriminals may target safety systems on purpose. They seek to disable alarms, valve controls, and other protections.
- Physical damage: By tampering with ICS settings, attackers can directly damage physical equipment like turbines, reactors, pipelines, and other critical infrastructure. Altering configurations outside safe limits stresses equipment. It stresses it in ways it wasn't designed to handle. This leads to premature wear, fractures, warping, and other damage.
- Financial Losses: Between production downtime, equipment repairs, regulatory fines, and mitigation costs, a single cyber-attack easily racks up massive financial losses. A 2021 report found that the average cost of ICS intrusions was over $6.9 million per incident. Some big attacks have cost the affected company hundreds of millions. Cyber-attacks represent a major financial risk.
Security Best Practices
These systems have unique cybersecurity challenges. They are due to their complexity and need for real-time operation. Yet, organizations can take steps to harden their ICS environments against threats.
Some best practices include:
- Network segmentation and monitoring: ICS networks should be physically and logically separated from other networks through firewalls, DMZs, and VLANs. This limits access and prevents malware from spreading. Network traffic should be continuously monitored to detect anomalies.
- Access control and authentication: Strict access controls via role-based access, multi-factor authentication, and the principle of least privilege prevent unauthorized access. Accounts, credentials, and permissions should be reviewed regularly.
- System hardening: Unused ports/services should be disabled and vendor default accounts/passwords changed. Systems should be configured securely, following guidelines like IEC 62443. Antivirus, file integrity monitoring, and application whitelisting further harden systems.
- Patch management: Regular patching of operating systems, ICS applications, and other software is essential. Risk assessments determine the speed of patching based on criticality. Test systems validate patches before deployment.
- Incident response planning: Comprehensive incident response plans with defined roles, procedures, and communications enable rapid containment and recovery from cyber incidents. ICS-specific considerations are vital. Regular drills keep plans effective.
Following best cybersecurity practices helps, and they are tailored to ICS environments. They greatly improve resilience against modern cyber threats.
Leveraging both organizational policies and technical controls provides defense-in-depth.
Choosing Security Solutions
Industrial control systems require specialized cybersecurity solutions to protect against threats.
Some key technologies to consider include:
- Firewalls and IDS/IPS create barriers between the ICS network and other networks. Intrusion detection and prevention systems monitor traffic for malicious activity and block attacks. Firewalls and IDS/IPS for ICS understand industrial protocols. They can filter traffic while allowing critical communications.
- SIEM: Security Information and Event Management (SIEM) solutions gather and analyze log data from ICS components. They do this to find oddities and threats. SIEM optimized for ICS can interpret industrial protocol logs.
- Endpoint detection: EDR monitors devices on the ICS network. It looks for malicious activity and unauthorized changes. EDR works well with ICS, which understands expected baseline behaviors.
- Backup and recovery: Backing up ICS configurations and data often allows recovery after an attack. Test backups periodically to verify they're working correctly. Use air-gapped backups that are isolated from the network for greater protection.
- Risk assessments: Conducting periodic risk assessments of the ICS environment provides visibility into vulnerabilities and guides investments in security measures. Include both internal assessments and independent third-party assessments.
Carefully evaluate ICS cybersecurity products. Check if they can join existing systems. Also, see how they will affect operations.
Prioritize solutions that provide visibility and protection without disruption. Work with vendors experienced in ICS environments.
Employee Training
A cybersecurity program is only as strong as its weakest link. That's why ongoing cybersecurity training and testing for employees is crucial.
- Security awareness: Employees should complete regular security awareness training to learn about the latest cyber threats, phishing techniques, safe practices, and their responsibilities. Training should cover topics. These topics include: password hygiene, social engineering, physical security, and incident reporting.
- Phishing simulations: One of the most common attack vectors is phishing emails. Running regular simulated phishing campaigns helps train employees. They learn to identify and avoid real phishing attempts. Stats from the simulations also show which users need additional training.
- Proper access controls are key: Access should be limited to only what an employee's role needs. Rights like remote access and admin privileges should be tightly controlled. Employees should understand the risks of excessive permissions.
- Reporting vulnerabilities/incidents: Employees should know how to properly report any suspicious activity, vulnerabilities, or incidents like a potential breach. Clear reporting procedures allow the security team to respond quickly to minimize damage.
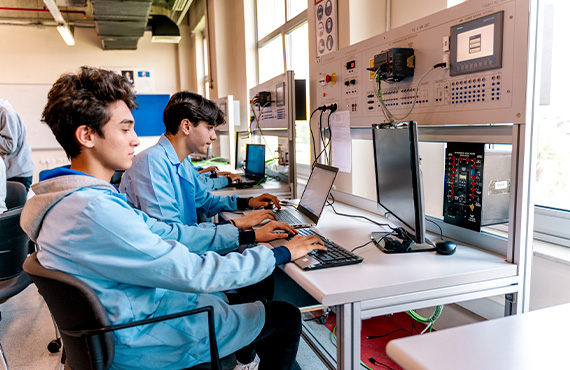
Key Takeaways
ICS are crucial. They keep operations smooth in process automation facilities.
But, they can also present cybersecurity risks if not properly protected. This blog post sums up the main threats to ICS. They include malware, ransomware, phishing attacks, and insider threats. Real-world attacks like Stuxnet and TRITON show how motivated attackers can disrupt critical infrastructure. To reduce these risks, organizations should use layered security. They should focus on system hardening, network segmentation, access controls, and encryption.
Ongoing security awareness training for employees is also key to reducing human-error vulnerabilities. By being proactive in ICS cybersecurity, you can protect infrastructure from attack. The potential consequences of a breach are too severe not to make ICS security a top priority.
Contact Proconex today to learn about our trusted solutions for every stage of your OT/IT and ICS cybersecurity journey!