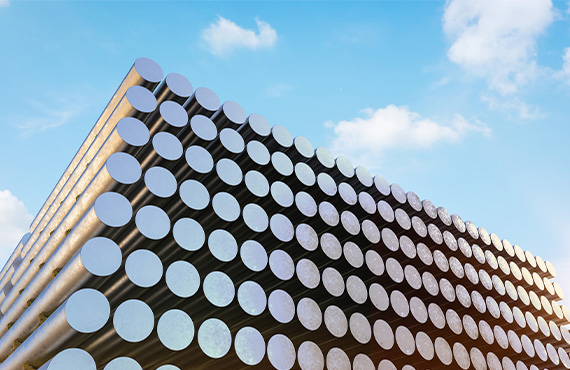
In the manufacturing of metals margins are tight and costs are high. Metals companies need to maximize efficiency and productivity at every step. One way to do this is by using an effective machine condition monitoring program.
Machine condition monitoring uses sensors and analytics. They track the health of critical equipment like motors, pumps, and gearboxes. Knowing how these assets are doing now can help metals companies. It lets them move from fixing problems to predicting them. This allows them to prevent breakdowns. It helps them to plan maintenance better. And it improves their operational insights.Predicting problems before they happen lets you avoid costly downtime. It also helps you maintain top performance.
With a detailed overview of equipment health, you can start better maintenance programs. Real-time tracking also allows for energy optimization and reduced consumables usage.
Today, in the metals industry, monitoring machine condition is essential. An effective monitoring program provides operational insights. These programs are needed to cut costs, maximize uptime, and boost productivity.
What is Machine Condition Monitoring?
MCM is the ability to assess the health of a machine over a period of time. This can include things like the machine’s efficiency. Losses in efficiency may indicate an underlying issue. It also asses wear-and-tear on parts, performance indicators such as output of defective parts, usage statistics, and maintenance statistics. The goal of MCM is to identify issues and changes in the machine's operation and health.
MCM works by installing sensors on key machine parts: these include bearings, gears, and motors. The sensors record data on the machine's condition, performance, and environment continuously.
This data is aggregated and analyzed using specialized software platforms. We use data analytics, pattern recognition, and algorithms. These software platforms help us find problems early. By analyzing the data trends, experts can find signs of wear. They can also find signs of misalignment, looseness, and overheating.
Finding issues early gives companies time to fix them with predictive maintenance. This is before the issues cause catastrophic failure.
Why Machine Condition Monitoring Matters in the Metals Industry
The complex industrial processes in the metals industry involve large equipment, such as furnaces, rolling mills, and casting machines. These assets are exposed to extreme conditions. These include high temperatures, heavy loads, and abrasive or corrosive materials. As a result, they experience significant wear and tear over time.
Without proactive maintenance and monitoring, these assets can perform poorly and get sick. This leads to more unexpected downtime, lost production, and safety risks. For metals companies, avoiding disruptions is crucial. This is because their production is continuous.
By using machine condition monitoring, metals companies can shift from reacting to maintaining. Instead of waiting for failures to occur, they can detect emerging issues early.
This allows for planned repairs and predictive maintenance before problems escalate. Keeping equipment in top working order has many benefits. These include better uptime, throughput, product quality, and safety.
Key Benefits for Metals Companies
The metals industry is very demanding. It comes with high temperatures, continuous operation, heavy loads, and exposure to contaminants. These factors push equipment to its limits. Further, this causes many breakdowns, failures, and unplanned downtime. These problems impact productivity and profitability.
Implementing a machine condition monitoring program provides powerful benefits for metals companies:
- Reduced downtime: Real-time monitoring detects emerging issues early, before they cause catastrophic failure. Companies can schedule maintenance at opportune times, avoiding disruptive downtime.
- Increased productivity: With fewer breakdowns and failures, overall equipment effectiveness is maximized. Companies produce more high-quality output from their assets.
- Optimized maintenance: Instead of time-based maintenance, companies can adopt condition-based strategies. Maintenance is performed when needed, not on a fixed schedule.
- Improved safety: By detecting problems ahead of time, major failures that could harm workers are avoided. Condition monitoring enhances the safety of personnel.
Machine condition monitoring transforms maintenance from a cost center to a profit driver. Metals companies can leverage operational insights to maximize uptime, yield, and margins.
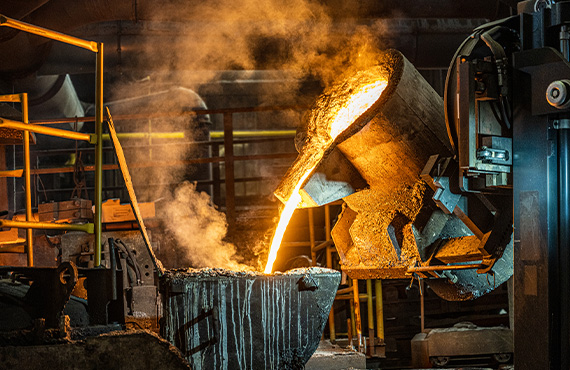
MCM Insights for the Metals Industry
Monitoring machine condition gives metals companies invaluable insights. They can drive big improvements. Here are some of the key types of insights that you can obtain:
- Production efficiency: By closely monitoring critical equipment like mills, presses, and furnaces, metals companies can identify performance dips and production bottlenecks. This allows for adjustments to be made to optimize efficiency and throughput. The data can also reveal which machines have chronic issues. These issues need more basic fixes.
- Equipment health: Continuous monitoring provides an ongoing picture of equipment health. Subtle changes and anomalies can be detected early. They can lead to costly, unplanned downtime and repairs. Being proactive preserves asset lifespan.
- Preventative maintenance needs: The condition data makes clear which assets need maintenance and when. Then, maintenance can be scheduled based on need and urgency, not guesses. This reduces maintenance costs and disruptions.
- Energy consumption: Many assets like furnaces are major energy hogs. We monitor to find chances to adjust operations. This cuts energy waste and utility bills.
Implementing a Condition Monitoring Program
Adopting an effective machine condition monitoring program requires careful planning and execution. Here are the key steps you should follow:
- Assess goals and needs. What assets need monitoring? What data do you want to track? How will insights be used? This helps guide technology selection.
- Survey equipment and infrastructure. Catalog all critical assets and determine monitoring capabilities. Can systems be retrofitted or need full upgrades?
- Select optimal technologies. Vibration sensors, infrared thermography, ultrasonics, lubricant analysis, and other solutions each have advantages. Choose what fits your needs and assets.
- Strategically install monitors and sensors. Place them on vital machines like kilns, presses, and rolling mills. Prioritize problem areas.
- Integrate with data infrastructure. Monitoring systems should connect to plant data networks. They should also connect to historian platforms to enable analytics.
- Develop reporting workflows. Configure how data is analyzed, translated into insights, and shared with stakeholders. Automate where possible.
- Train personnel. Educate staff on interpreting outputs, investigating issues, and utilizing insights. Document processes and findings.
- Continuously optimize. Fine-tune monitoring capabilities and outputs. Add assets and new technologies. Leverage learning to maximize benefits.
- Maintain and update systems. Keep technologies and infrastructure current. Audit programs regularly for improvement opportunities.
By planning carefully and executing with discipline, you can use condition monitoring to gain invaluable insights. You can do this across your facilities.
Choosing the Right Solution Provider
When evaluating partners for a machine condition monitoring solution, it's important to find a provider with deep expertise and proven tech. The ideal partner will have experience with condition monitoring. They will also have used it across a wide variety of assets and processes in the metals industry.
Look for the following capabilities in a solutions provider:
- Extensive knowledge of equipment, processes, and challenges common in metals companies. Domain expertise is crucial.
- A comprehensive portfolio of sensing technologies like vibration monitoring, thermography, ultrasonics, and more. A mix of technologies is key for holistic monitoring.
- Advanced analytics and AI to turn data into actionable insights. Look for automated analytics and prediction capabilities.
- Secure data management tools to collect, analyze, and visualize information in one place. Integrated platforms add value.
- Global service and support infrastructure to ensure maximum uptime and performance. Local expertise matters.
- Experience driving quantifiable results like improved quality, increased throughput, and reduced downtime. Proven ROI is ideal.
The right partner understands the metals industry well. They can customize MCM solutions to meet your specific goals. With their guidance, you can unlock game-changing insights. They will take your performance to new heights.
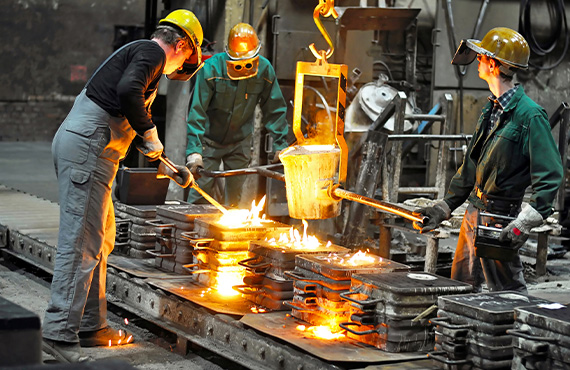
Start Unlocking Operational Insights
Operational insights are within reach with the right machine condition monitoring solution. Don't leave this powerful opportunity on the table. Contact the experts at Proconex today. Learn how Emerson's better monitoring tech can reveal big insights. Our team is highly skilled at setting up full condition monitoring programs. We'll do a thorough needs assessment. Then, we'll create a custom solution using Emerson's top technologies.
You'll gain operational visibility like never before. This is thanks to real-time monitoring, predictive analytics, and actionable recommendations. Our solutions are proven to cut unplanned downtime. They also improve asset use, lower maintenance costs, and boost production efficiency.
See the difference machine condition monitoring can make. Reach out now to schedule a demo and discuss your operational goals with our team. The first step toward unlocking your operational insights starts here!