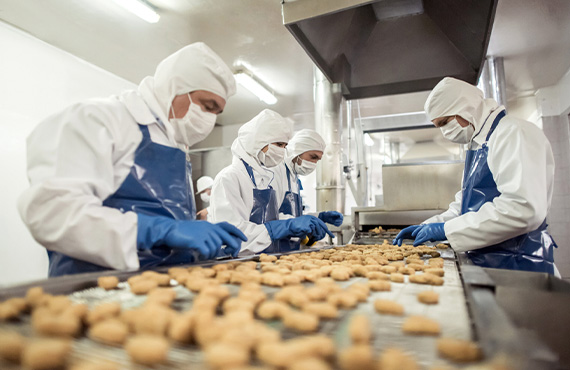
As a food and beverage manufacturer, ensuring the highest quality standards is paramount.
Your products directly impact consumer health and safety, making quality control an essential aspect of your operations. However, maintaining consistent quality across complex production processes can be a daunting challenge.
Imagine a scenario where a batch of your products fails to meet stringent quality requirements. This could lead to costly product recalls, damaging your brand reputation and eroding consumer trust. Even worse, quality lapses could result in food safety incidents, posing serious health risks to your customers. The consequences of such events can be devastating, potentially leading to legal liabilities, financial losses, and irreparable damage to your company's credibility.
Further, quality issues can manifest in various forms, such as inconsistent taste, texture, or appearance, impacting customer satisfaction and loyalty. In a highly competitive market, even minor deviations from expected quality standards can drive consumers towards alternative brands, resulting in lost market share and revenue.
Addressing these challenges requires a proactive and data-driven approach to quality control. Traditional methods, while valuable, may not provide the real-time insights and predictive capabilities necessary to stay ahead of potential quality issues. This is where advanced process analytics and machine learning can revolutionize your quality control efforts, empowering you to maintain the highest standards while optimizing your production processes.
Limitations of Traditional Quality Control Methods
Traditional quality control methods in food and beverage manufacturing, such as manual inspections, sampling, and offline testing, have several limitations that can hinder the ability to maintain consistent product quality and minimize waste. These methods are often labor-intensive, time-consuming, and prone to human error, making it challenging to detect and address quality issues in real-time.
Manual inspections rely on human observation, which can be subjective and inconsistent, leading to variations in quality assessments. Additionally, these inspections are typically performed on a small sample of the production batch, leaving room for undetected defects or quality issues in the remaining products.
Offline testing, where samples are sent to a laboratory for analysis, can provide valuable insights into product quality, but the process is inherently delayed. By the time the results are available, a significant portion of the production run may have already been completed, potentially resulting in the need to discard or rework a large quantity of non-conforming products.
In addition, traditional quality control methods often lack the ability to provide comprehensive, real-time insights into the manufacturing process itself. They primarily focus on the end product, making it difficult to identify and address the root causes of quality issues proactively.
In today's highly competitive and regulated food and beverage industry, these limitations can lead to increased waste, production inefficiencies, and potential compliance issues, ultimately impacting profitability and customer satisfaction. To overcome these challenges, manufacturers are recognizing the need for more advanced, data-driven approaches that can provide real-time process monitoring, predictive analytics, and continuous process optimization.
The Power of Advanced Process Analytics and Machine Learning

In the era of Industry 4.0, advanced process analytics and machine learning are emerging as game-changers for quality control in food and beverage manufacturing. These cutting-edge technologies have the potential to revolutionize the way you monitor, analyze, and optimize your production processes, enabling you to achieve unprecedented levels of product quality, efficiency, and sustainability.
With advanced process analytics, you can leverage the power of big data and sophisticated algorithms to gain deep insights into your manufacturing processes. By collecting and analyzing vast amounts of data from various sources, such as sensors, control systems, and historical records, you can uncover hidden patterns, trends, and relationships that would be nearly impossible to detect through traditional methods.
Machine learning takes this a step further by enabling your systems to learn and adapt from the data, continuously improving their ability to detect anomalies, predict outcomes, and make informed decisions. These algorithms can identify complex correlations and patterns that human analysts might miss, allowing for more accurate and timely interventions to maintain product quality and prevent defects.
Also, the combination of advanced process analytics and machine learning opens up new possibilities for predictive analytics and process optimization. By analyzing historical data and real-time process parameters, these technologies can forecast potential quality issues, enabling you to take proactive measures to mitigate risks and minimize waste. Additionally, they can identify opportunities for process improvements, suggesting adjustments to variables such as temperature, pressure, or ingredient ratios to optimize efficiency, reduce costs, and enhance product quality.
With the power of advanced process analytics and machine learning at your fingertips, you can transform your quality control approach from reactive to proactive, empowering you to stay ahead of potential issues and continuously refine your processes for superior results.
Real-time Process Monitoring and Anomaly Detection
One of the key advantages of leveraging advanced process analytics and machine learning in food and beverage manufacturing is the ability to monitor critical process parameters in real-time. By collecting and analyzing data from various sensors, instruments, and control systems, you can gain a comprehensive understanding of your production processes as they unfold.
Advanced analytics algorithms can continuously analyze this data stream, identifying patterns, trends, and deviations from normal operating conditions. This real-time monitoring capability enables you to detect anomalies and potential quality issues before they escalate, allowing for proactive interventions and corrective actions.
Imagine being able to monitor the temperature, pressure, flow rates, and other critical parameters across your entire production line, with machine learning models constantly evaluating the data for any deviations from expected norms. If an anomaly is detected, such as a sudden temperature spike or a drop in pressure, the system can immediately alert your quality control team, enabling them to investigate the root cause and take necessary actions to prevent defective products from being produced.
Not to mention, these advanced analytics solutions can integrate data from multiple sources, providing a holistic view of your manufacturing processes. By correlating data from different stages of production, you can identify interdependencies and potential bottlenecks, enabling you to optimize your operations and ensure consistent product quality.
With real-time process monitoring and anomaly detection, you can significantly reduce the risk of quality issues, minimize waste, and ensure that your products meet the highest standards of safety and quality. By leveraging the power of advanced analytics and machine learning, you can transform your quality control approach, moving from reactive to proactive, and ultimately delivering superior products to your customers.
Predictive Analytics and Quality Forecasting
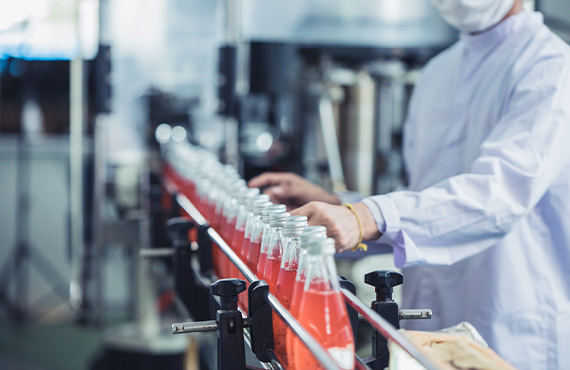
Quality forecasting is a game-changer in the food and beverage industry. By leveraging historical data and advanced machine learning models, you can predict future quality outcomes with remarkable accuracy. Imagine being able to anticipate potential quality issues before they even occur, allowing you to take proactive measures and make necessary process adjustments.
The key lies in harnessing the power of your manufacturing data. Every batch, every production run, and every quality check generates a wealth of information that can be transformed into valuable insights. By feeding this data into sophisticated predictive analytics algorithms, you can uncover hidden patterns, correlations, and trends that would otherwise go unnoticed.
These predictive models can analyze a wide range of factors, including raw material characteristics, environmental conditions, equipment performance, and process parameters. By understanding how these variables interact and influence quality, you can make informed decisions to optimize your processes and maintain consistent product quality.
But, predictive analytics goes beyond mere forecasting. It also enables you to simulate different scenarios and explore the potential impact of various process adjustments. This "what-if" analysis empowers you to experiment safely, without risking costly production runs or compromising quality.
Plus, predictive analytics can be integrated into your existing quality control systems, providing real-time alerts and recommendations. Imagine receiving an early warning about a potential quality deviation, allowing you to take immediate corrective action and prevent costly product losses or recalls.
By embracing predictive analytics and quality forecasting, you can transform your quality control approach from reactive to proactive, ensuring consistently high product quality, minimizing waste, and maximizing operational efficiency.
Process Optimization and Continuous Improvement
Harnessing the power of advanced process analytics and machine learning goes beyond just monitoring and detecting anomalies. The true potential lies in leveraging the data-driven insights to optimize your production processes continually, reduce waste, and drive ongoing improvements in quality and efficiency.
With real-time visibility into every aspect of your operations, you can identify bottlenecks, inefficiencies, and areas for improvement that may have gone unnoticed before. By analyzing the vast amounts of data generated by your manufacturing processes, you can uncover patterns, correlations, and root causes that impact product quality and yield.
Advanced analytics algorithms can then be employed to simulate different scenarios and test various process adjustments, allowing you to make informed decisions about optimizing parameters such as temperature, pressure, flow rates, and ingredient ratios. This data-driven approach eliminates the guesswork and trial-and-error methods of the past, enabling you to fine-tune your processes with precision and confidence.
Besides, the continuous nature of advanced process analytics means that as your operations evolve, the system adapts and learns, constantly refining its models and recommendations. This ensures that your quality control measures remain relevant and effective, even as new products, ingredients, or production methods are introduced.
By embracing a culture of continuous improvement driven by data-driven insights, you can consistently minimize waste, reduce production costs, and deliver superior quality products that meet or exceed customer expectations. This proactive approach to quality control not only enhances your bottom line but also strengthens your brand reputation and customer loyalty in an increasingly competitive market.
Get Started with Advanced Process Analytics
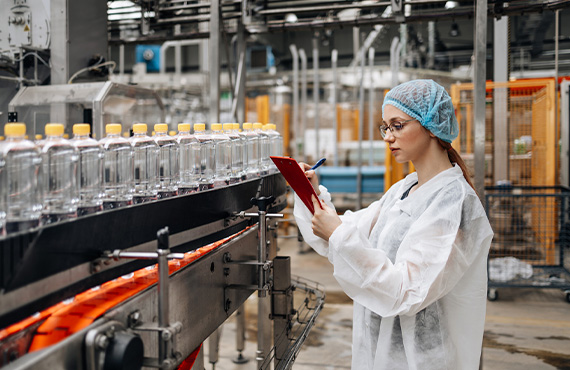
Are you ready to unlock the full potential of data-driven quality control in your food and beverage manufacturing operations? Implementing advanced process analytics and machine learning may seem daunting, but with the right approach, it can be a game-changer for your business. Here are some practical steps to get you started:
- Assess Your Data Readiness: Evaluate the quality, completeness, and accessibility of your existing process data. Identify gaps and implement measures to ensure consistent and accurate data collection across your operations.
- Establish Clear Goals and Priorities: Define your specific quality control objectives, such as reducing defects, minimizing waste, or optimizing yield. Prioritize the areas where advanced analytics can deliver the most significant impact.
- Build a Cross-Functional Team: Assemble a diverse team that includes process engineers, data scientists, quality experts, and operations personnel. Foster collaboration and knowledge sharing to ensure successful implementation and adoption.
- Select the Right Tools and Technologies: Evaluate various advanced analytics platforms, considering factors like scalability, integration capabilities, and user-friendliness. Look for solutions that offer robust machine learning algorithms and intuitive data visualization tools.
- Start Small and Iterate: Begin with a pilot project focused on a specific process or product line. This approach allows you to validate the technology, refine your strategies, and build confidence before scaling up across your operations.
- Invest in Training and Change Management: Ensure that your team members are well-trained in the new technologies and processes. Develop a comprehensive change management plan to facilitate smooth adoption and overcome any resistance to new methods.
- Continuously Monitor and Optimize: Advanced process analytics is an ongoing journey. Regularly review your results, identify areas for improvement, and refine your models and strategies to stay ahead of evolving quality control challenges.
Remember, successful implementation of advanced process analytics and machine learning requires a combination of the right technology, skilled personnel, and a data-driven culture. By following these guidelines and embracing a continuous improvement mindset, you can transform your quality control processes and stay competitive in the ever-evolving food and beverage manufacturing landscape.
The Role of Proconex in Quality Control Transformation
As a leading provider of industrial automation and process control solutions, Proconex is at the forefront of helping food and beverage manufacturers harness the power of advanced process analytics and machine learning for quality control transformation. With decades of experience and a team of highly skilled engineers and data scientists, Proconex offers a comprehensive suite of solutions tailored to the unique needs of the food and beverage industry.
Proconex's expertise lies in seamlessly integrating cutting-edge technologies, such as advanced process analytics, machine learning, and industrial internet of things (IIoT), into existing manufacturing processes. Our solutions enable real-time monitoring, predictive analytics, and process optimization, empowering manufacturers to achieve unprecedented levels of product quality, reduce waste, and optimize production efficiencies.
To Summarize
As you've seen, advanced process analytics and machine learning offer a transformative approach to quality control in food and beverage manufacturing. By harnessing the power of real-time data analysis, predictive modeling, and process optimization, you can dramatically improve product quality, reduce waste, and streamline operations.
Imagine a future where every batch is produced with precision, every deviation is detected instantly, and every process is optimized for maximum efficiency. This is the future that Proconex can help you achieve.
Don't let outdated quality control methods hold your business back. Take the first step towards a data-driven, proactive approach to quality management. Explore Proconex's cutting-edge solutions or schedule a consultation with our experts today. Together, we can revolutionize your manufacturing processes and unlock new levels of quality, efficiency, and profitability.