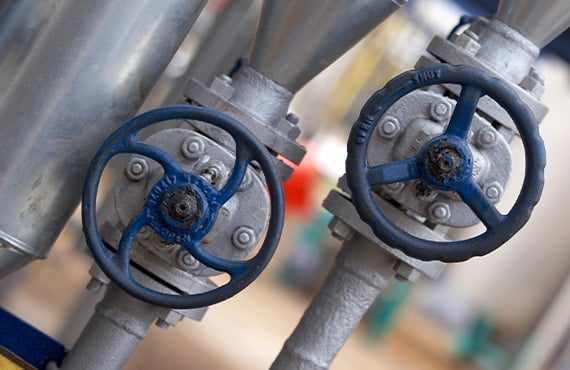
In the world of industrial maintenance and reliability, one question looms large: how can we reduce or even prevent unplanned downtime?
The answer might lie in the realm of modern valve diagnostics, a proactive approach that can spell the difference between a smooth-running operation and costly shutdowns.
This blog explains how innovative valve diagnostics, particularly those leveraged by Proconex using Emerson's cutting-edge tools, are revolutionizing predictive maintenance strategies.
Understanding Valve Diagnostics
Before we get ahead of ourselves, let’s take a step back to understand what we mean by valve diagnostics. Essentially, valve diagnostics involves the use of advanced tools and technologies to monitor valve performance. The goal? To detect any signs of wear, degradation, or failure before they lead to larger, system-wide problems. Ultimately, these problems will lead to unplanned downtime in your facility or facilities.
The Impact of Unplanned Downtime
When your plant experiences unplanned downtime, it triggers a series of challenges and consequences that can significantly impact various aspects of your operations. Unplanned downtime is when production halts unexpectedly due to equipment failures, supply chain issues, human error, or other unforeseen problems. Here’s what typically happens:
- Lost Production: The most immediate impact of unplanned downtime is the cessation of production. This means no products are being manufactured, assembled, or processed, leading to delays in fulfilling orders and potential revenue loss.
- Increased Costs: Unplanned downtime often incurs additional costs. These can include the expense of emergency repairs, overtime pay for technicians working to resolve the issue, and the potential need for expedited shipping to meet deadlines once production resumes.
- Operational Disruption: The workflow across the plant is disrupted. This can affect not just the immediate production line but also upstream and downstream processes. Schedules need to be rearranged, and resources reallocated, causing a domino effect of inefficiency across operations.
- Customer Dissatisfaction: Delays in production can lead to missed delivery deadlines, affecting customer satisfaction and trust. This can harm your company's reputation and lead to lost business if customers decide to seek more reliable suppliers.
- Employee Morale: Frequent unplanned downtime can be demoralizing for employees. It disrupts their work, might necessitate overtime or idle time, and can create a stressful environment, especially if there's pressure to catch up once production resumes.
- Wasted Resources: Materials may go to waste, especially if you’re dealing with perishable goods or if the production process cannot be paused without spoiling or damaging in-progress work. Energy resources are also wasted if machines are left in standby mode without producing anything.
- Data and Insight Loss: When production stops suddenly, the opportunity to collect operational data and insights is lost. Continuous operation and monitoring help in refining processes and improving efficiency, which are halted during downtime.
- Safety Risks: Restarting production after an unplanned stoppage can pose safety risks. Rushing to make up for lost time might lead to shortcuts or overlooking safety protocols, endangering workers.
- Compliance Issues: For industries subject to strict compliance and regulatory standards, unplanned downtime can jeopardize compliance, especially if it results in rushed production or missed quality checks.
Unplanned downtime is a costly and disruptive event that every plant wants to avoid or minimize.
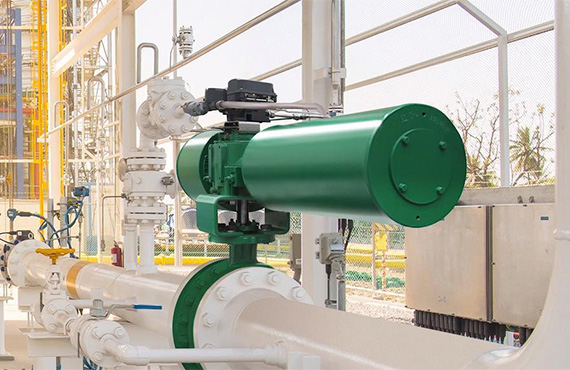
Embracing Predictive Maintenance with Proconex Emerson Tools
Proconex has been at the forefront of integrating Emerson's suite of valve diagnostic tools such as controllers and instruments into our service offerings. But how exactly does this technology work to prevent unexpected shutdowns? Let’s break it down:
- Early Problem Detection: By continuously monitoring valve performance, these tools can identify minor issues before they escalate.
- Health and Performance Insights: Detailed analytics provide a comprehensive overview of valve conditions, signaling when maintenance is necessary.
- Preemptive Action: Armed with this information, engineering teams can intervene early, repairing or replacing components as needed to avoid larger failures.
The Proconex Family
The Proconex family includes Atlantic Valve Services and Valspec, both integral to delivering exceptional maintenance solutions. By pooling our resources and expertise, we offer unrivaled support to their clients.
Proconex’s Approach to Engineering Maintenance Solutions
With over 75 years in the business, Proconex is not just another service provider. We are the exclusive Emerson Impact Partner for Emerson Automation Solutions in the Mid-Atlantic region. Here’s what sets us apart:
- Comprehensive Portfolio: Offering everything from process automation control systems to valves and measurement instrumentation.
- Industry-Wide Expertise: Serving a broad range of sectors, including Life Sciences, Chemical, Power, and more.
- Dedication to Excellence: With a keen focus on safety, quality, and delivering top-notch services.
The Bottom Line: Is It Time to Invest in Valve Diagnostics?
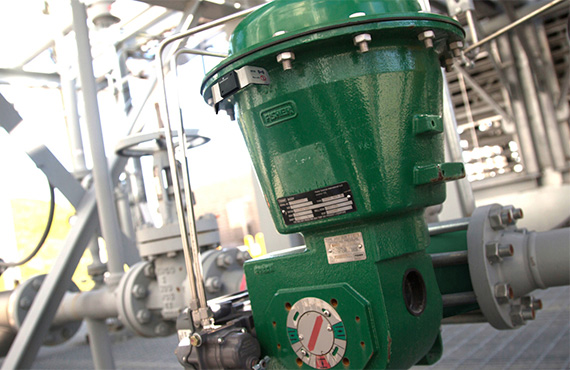
Now, let’s consider the original question: can modern valve diagnostics save your plant from unplanned downtime? The evidence suggests a resounding yes. By adopting these technologies, facilities can not only foresee potential issues but also enact measures to prevent them, ensuring smoother, more reliable operations.
So, ask yourself: Is your facility adequately equipped to predict and prevent unplanned downtime? If you're still relying on reactive maintenance strategies, it might be time to explore what Proconex and modern valve diagnostics can do for you.
Remember, in today's competitive landscape, the ability to maintain continuous, efficient operations is not just an advantage—it's a necessity.
FAQs: Modern Valve Diagnostics and Proconex Solutions
Valve diagnostics involves using advanced technologies to monitor, assess, and analyze the performance and condition of industrial valves. This method helps identify issues like wear, potential failures, or inefficiencies that could impact system performance and lead to unplanned downtime.
Valve diagnostics allow for the early detection of problems that could cause operational interruptions. By understanding valve performance and anticipating failures before they occur, companies can schedule maintenance or repairs during planned downtimes, thus avoiding unexpected outages and costly disruptions.
Proconex leverages Emerson's sophisticated diagnostic tools as part of our maintenance and service offerings. These tools are designed to provide detailed analytics and performance data, enabling precise monitoring and timely interventions.
Yes, predictive maintenance can significantly enhance plant uptime by addressing potential issues before they escalate into serious problems. This approach shifts the focus from reactive to proactive maintenance, which not only preserves equipment but also optimizes the overall operational efficiency.
Proconex offers solutions across a diverse range of sectors including Life Sciences, Chemical, Power, Refining, Oil & Gas, Food & Beverage, Paper, Metals, and more. We also cater to commercial enterprises and campus facilities, providing tailored services that meet specific industry demands.
Proconex has over 75 years of experience in providing engineering maintenance solutions. As the exclusive Emerson Impact Partner in the Mid-Atlantic region, we have access to leading-edge Emerson technologies along with a comprehensive portfolio of process automation control systems, valves, and control devices. Our commitment to safety, quality, and service excellence makes them a reliable partner in industrial maintenance.
The Proconex family includes Atlantic Valve Services and Valspec, both of which specialize in valve services and solutions. Our companies collaborate to provide wide-ranging expertise and enhanced service capabilities to our clients.
You can contact Proconex directly through our website or by phone. Our team of experts will be able to provide a consultation, assess your specific needs, and recommend the best solutions tailored to your industry and operational requirements.
By addressing these commonly asked questions, Proconex aims to demonstrate not only our expertise in valve diagnostics and preventive maintenance but also our ability to provide superior, client-focused solutions that enhance plant reliability and efficiency.