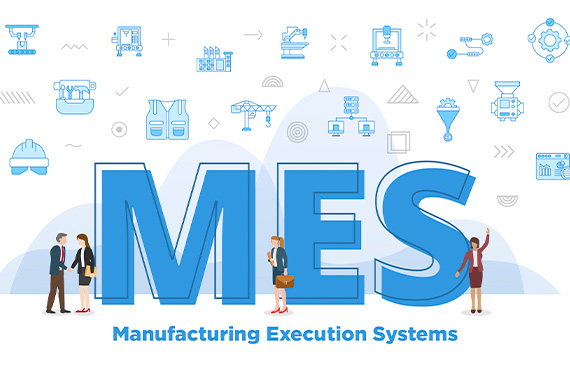
Manufacturing Execution Systems, also known as MES, are essential, management level tools in modern manufacturing operations. They are designed to monitor and control complex production processes, ensuring that manufacturing runs smoothly from order release to product delivery.
MES software acts as a bridge between the shop floor and the highest-level enterprise systems, providing real-time insights into production activities and improving efficiency and quality.
In this article, we'll explore the key functions and benefits of MES, as well as discuss emerging trends that are shaping this technology. Whether you're looking to streamline operations or boost productivity, understanding MES can greatly benefit manufacturers striving for operational excellence.
Understanding Manufacturing Execution Systems
When exploring manufacturing technologies, you might wonder, what are MES systems? An MES is an information system that actively monitors, tracks, documents, and controls the intricate processes involved in manufacturing operations.
Core Functions of MES:
1. Tracking Production Processes
MES provides real-time visibility into what is happening on the shop floor. From managing production schedules to monitoring equipment status, it ensures everything runs smoothly.
2. Managing Quality
Quality control is vital in manufacturing. MES integrates quality management systems to track defects, manage corrective actions, and ensure compliance with quality standards.
3. Handling Work Orders
Efficient handling of work orders is crucial for operational efficiency. MES automates work order management by prioritizing tasks and allocating resources effectively.
MES Systems Drive Digital Manufacturing Transformation and Growth
In the context of digital transformation trends, MES plays an instrumental role in modernizing manufacturing operations. By digitizing the production floor, manufacturers can leverage real-time data analytics to improve decision-making processes. This shift enables manufacturers to transition from traditional methods to more agile and efficient operations.
Through its comprehensive functionalities, MES bridges the gap between business systems like Enterprise Resource Planning (ERP) and plant floor operations. This integration facilitates seamless data flow across the organization, ensuring that every department—from procurement to production—works cohesively towards common goals.
As you explore these facets of MES, it's evident how this system can transform your manufacturing landscape into a digitally driven powerhouse.
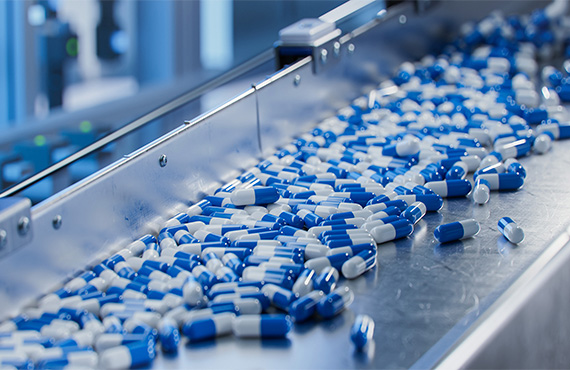
The Role of MES in Compliance Documentation
Meeting compliance requirements for MES systems is crucial, especially in regulated industries such as pharmaceuticals, aerospace, and food and beverage. These sectors rely heavily on accurate data and stringent documentation to meet industry standards and legal mandates. An MES can be a game changer in achieving these goals.
Key Compliance Benefits of MES:
Electronic Record Keeping: MES systems provide robust electronic record-keeping capabilities, replacing traditional paper-based methods. This not only ensures accuracy and reliability but also facilitates easy access and retrieval of important documents.
Traceability: With an MES, manufacturers can track every step of the production process. This traceability ensures that all compliance-related actions are documented, enabling quick audits and reviews.
Automated Documentation: Automating documentation through an MES minimizes human error, ensuring that all necessary records are captured and stored without manual intervention.
Audit Trails: MES solutions create comprehensive audit trails that document every change or update made to production processes. This level of detail is invaluable during compliance audits and helps in identifying potential areas of non-compliance quickly.
MES systems offer a structured approach to managing compliance, reducing the risk of penalties and recalls due to non-compliance issues. By leveraging these capabilities, manufacturers can focus on producing high-quality products while maintaining adherence to regulatory standards.
Integration with Other Industrial Automation Solution Systems
Understanding how an MES integrates with other systems is crucial for leveraging its full potential. MES often interacts with Enterprise Resource Planning ERP systems, the highest level of management systems, to enhance supply chain visibility. This seamless integration allows manufacturers to:
- Synchronize production schedules and inventory levels, ensuring materials are available when needed.
- Improve order tracking from initiation to completion, providing accurate delivery timelines.
- Streamline communication between departments, reducing errors and increasing efficiency.
- Additionally, connecting MES with SCADA systems or process control systems plays a vital role in real-time data exchange. This integration helps manufacturers by:
- Offering immediate insights into equipment performance and production metrics.
- Enabling proactive maintenance strategies through timely alerts and notifications.
- Facilitating better decision-making with up-to-date information on process variables.
The synergy between MES and these systems not only streamlines operations but also supports the digital transformation journey in manufacturing. Enhancing operational efficiency and transparency ensures that you stay competitive in the fast-paced industrial landscape.
What are the Benefits of Implementing MES?
Embracing a Manufacturing Execution System can transform your production line by improving flexibility and efficiency. Here are some key advantages:
Increased Equipment Uptime: With real-time monitoring and better work order management, MES systems ensure that equipment operates at peak efficiency. This minimizes unexpected breakdowns and extends the life of your machinery.
Reduced Downtime: Effective scheduling and predictive maintenance features help in planning repairs during non-productive hours, keeping your operations running smoothly.
Operational Agility: MES systems provide the flexibility to adapt quickly to changes in production demands or supply chain disruptions. This adaptability is crucial for maintaining competitiveness in today's fast-paced market.
Reduced Waste and Rework: By optimizing processes and ensuring quality control, MES helps minimize errors, leading to less scrap and fewer costly reworks.
Enhanced Manufacturing Operations Management: A comprehensive view of the shop floor allows managers to make informed decisions swiftly, improving both productivity and product quality.
Implementing an MES not only streamlines your manufacturing operations but also empowers you to meet customer expectations efficiently. As technology advances, these systems will continue to deliver even more impressive benefits.
Emerging Trends in Manufacturing Execution Systems
In the ever-changing world of modern manufacturing, AI and Machine Learning are transforming the capabilities of Manufacturing Execution Systems. These technologies enable MES to provide predictive analytics and automation features that significantly improve production efficiency.
1. Predictive Analytics
By using AI algorithms, MES can analyze large amounts of data from different production processes. This analysis helps predict potential problems such as equipment failures or quality deviations before they happen. Manufacturers can then proactively schedule maintenance, adjust, or allocate resources to minimize disruptions.
2. Automation
Machine learning enhances MES by improving decision-making processes. The system learns from past data and operational patterns, automating repetitive tasks. This not only speeds up production cycles but also reduces human errors. For example, an MES with machine learning can automatically adjust settings for optimal performance based on real-time conditions.
The integration of these advanced technologies within MES gives manufacturers a powerful tool to maintain smooth operations. By addressing potential challenges before they become major issues, companies can sustain high productivity levels while also ensuring quality and compliance. As AI and machine learning continue to develop, their role in shaping the future of MES is expected to grow, providing even deeper insights and efficiencies in manufacturing environments.
User Experience Enhancements in Modern MES Systems
1. Intuitive User Interfaces
Modern MES have evolved to prioritize user experience, particularly for shop floor operators who interact with these systems daily. The design of intuitive UI plays a crucial role in this evolution. Simplified navigation and clear visual indicators allow operators to quickly access vital information, reducing the time spent learning the system and enhancing productivity. These user-friendly interfaces ensure that even complex tasks can be managed efficiently without technical bottlenecks.
2. Augmented Reality Applications
The integration of augmented reality (AR) within MES software is transforming how operators approach complex manufacturing tasks. AR provides real-time guidance by overlaying digital information onto physical environments, offering step-by-step instructions or alerts directly through wearable devices or smart glasses. This technology aids in minimizing errors and accelerates training processes by allowing operators to visualize procedures and equipment interactions dynamically.
These advancements not only streamline operations but also contribute significantly to the What Are Manufacturing Execution Systems? Understanding the Role of MES narrative by showcasing how MES adapts to technological innovations to meet the demands of modern manufacturing environments. With these enhancements, MES continues to be an indispensable tool for driving efficiency and precision on the production floor.
Manufacturing Execution Systems are a game-changer for manufacturers looking to stay competitive in today's modern market. By connecting varying production processes and using digital to virtual technologies, MES helps manufacturers work more efficiently and effectively.
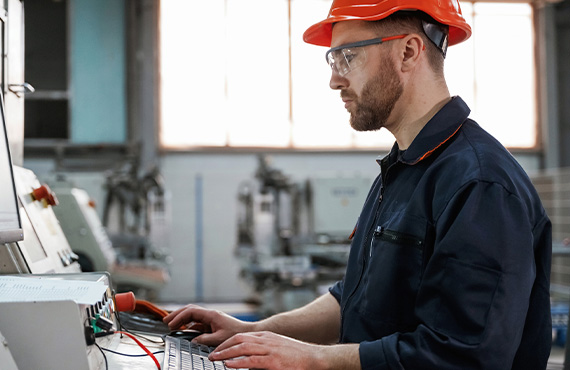
Why is MES Important for Manufacturing?
In the fast-paced world of modern manufacturing, using MES is crucial for survival and success. This technology gives businesses the power to deliver products accurately and efficiently. As manufacturers continue to innovate, MES will play a key role in shaping the industry's future.
Operational Excellence: MES makes workflows smoother, reduces mistakes, and optimizes resource use for top-notch performance.
Strategic Enabler: With real-time data insights, manufacturers can make quick decisions and stay ahead of market demands.
Competitive Edge: Implementing MES helps companies meet complex compliance standards and adapt to new industry trends quickly.
Are you ready to leverage Manufacturing Execution Systems for operational excellence? Explore Proconex’s offerings in detail. Our team specializes in creating MES solutions customized to your unique manufacturing requirements. Learn how we can assist you in implementing a system that not only addresses the question, “What is MES?” but also enhances your production capabilities. Contact us to discover our services aimed at transforming your manufacturing processes with accuracy and efficiency.