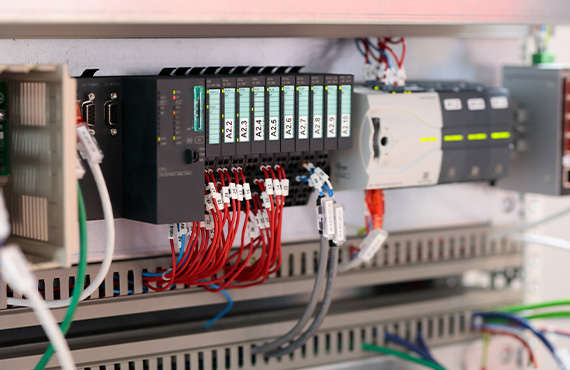
In the fast-paced world of business and industry, the efficiency and effectiveness of your operations can make all the difference between success and stagnation.
When it comes to optimizing your processes and maximizing productivity, investing in top-quality process automation control systems is crucial.
In this blog post, we will explore why prioritizing quality in your automation systems should be your top priority. So, let's get into the world of process automation control systems and uncover the importance of quality in driving your business forward.
What are Process Automation Control Systems?
Before we dive into the importance of quality, let’s define what Process Automation Control Systems are. In essence, Process Automation Control Systems are designed to automate and control various processes within a system. They use a combination of hardware and software components to monitor and control industrial processes, providing companies with a more accurate and efficient way of managing production lines.
Key components of a process automation control system include:
- Sensors and Instrumentation: These devices measure and monitor various process parameters such as temperature, pressure, flow rates, and levels, providing the system with real-time data.
- Programmable Logic Controllers (PLCs): PLCs are industrial computers that execute the control logic and algorithms, translating the input data from sensors into output signals that control actuators and other field devices.
- Human-Machine Interface (HMI): The HMI provides a graphical user interface that allows operators to monitor and interact with the system, visualize process data, and make adjustments as needed.
- Supervisory Control and Data Acquisition (SCADA): SCADA systems are responsible for collecting and processing data from multiple PLCs and other control systems, providing a centralized view of the entire operation.
- Communication Networks: Robust communication networks, such as Ethernet, fieldbus, or wireless systems, enable the exchange of data between various components of the automation system.
The Rise of Process Automation Control Systems
With technological advancements, process automation control systems have become an integral part of modern businesses. They have revolutionized industries worldwide, starting with manufacturing plants and quickly making their way to sectors such as chemical, food & beverage, power & energy, refining, and oil & gas.
The reason behind their success has been their ability to provide businesses with the tools to automate their processes, improving productivity while reducing manual labor and potential room for errors.
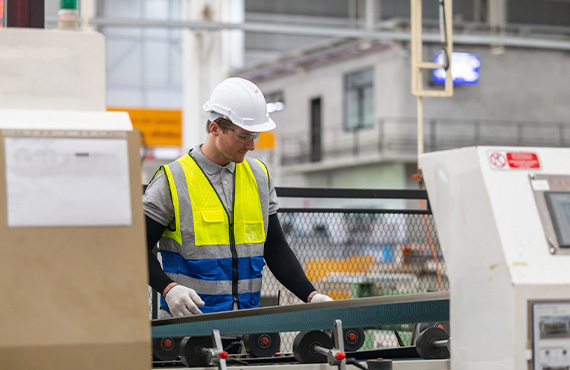
Dealing with Low-quality Process Automation Control Systems
When it comes to industrial production, process automation control systems (PACS) are the backbone of many companies, as they are responsible for ensuring that production runs smoothly and efficiently. PACS are an integral part of modern manufacturing operations, and choosing the right system is critical to the success of any company.
But, what happens when your Process Automation Control Systems are of low quality?
First and foremost, low-quality PACS can lead to production delays and downtime. If systems fail or malfunction due to subpar technology, production will inevitably come to a halt. This can result in a loss of revenue, missed deadlines, and an increase in operating costs. Maintaining high-quality PACS is critical to avoid these costly production delays.
Further, low-quality PACS can have a significant impact on product quality. Faulty systems may result in product defects, inconsistencies, and a lack of standardization. This can ultimately lead to dissatisfied customers, reduced brand loyalty, and decreased sales. Skimping on the quality of PACS can have far-reaching consequences that affect the bottom line.
Lastly, low-quality PACS can pose safety risks. Industrial production is a dangerous industry, and PACS are responsible for ensuring that equipment runs safely and effectively. Faulty systems can result in increased safety risks and accidents, putting employees and assets at risk.
High-quality PACS are a top priority for any company. Without them, production delays, poor product quality, and safety risks become all too common. It is imperative for companies to prioritize choosing reliable, sturdy equipment that is up to the task.
Choosing lower-quality options may seem like a way to save money in the short term, but it can ultimately lead to costly mistakes and losses down the line.
Impact on Productivity and Efficiency
Implementing a high-quality process automation control system can have a profound impact on productivity and efficiency within an organization. These systems are designed to streamline operations, minimize human errors, and optimize processes, ultimately leading to increased output and reduced operational costs.
One of the primary benefits of quality automation systems is the reduction of downtime. Traditional manual processes are susceptible to human errors, equipment failures, and other unforeseen circumstances that can lead to costly production stoppages. Automation systems, when designed and implemented correctly, can significantly mitigate these risks by continuously monitoring and adjusting processes in real-time, ensuring smooth and uninterrupted operations.
Moreover, quality automation systems enable organizations to optimize their processes by identifying bottlenecks, inefficiencies, and areas for improvement. Through data analysis and advanced algorithms, these systems can pinpoint opportunities for process optimization, leading to increased throughput, reduced waste, and improved resource utilization.
As a result, investing in quality process automation control systems can significantly boost productivity and efficiency within an organization. By reducing downtime, optimizing processes, improving product quality, and enabling better resource allocation, these systems offer a competitive advantage and contribute to long-term profitability and growth.
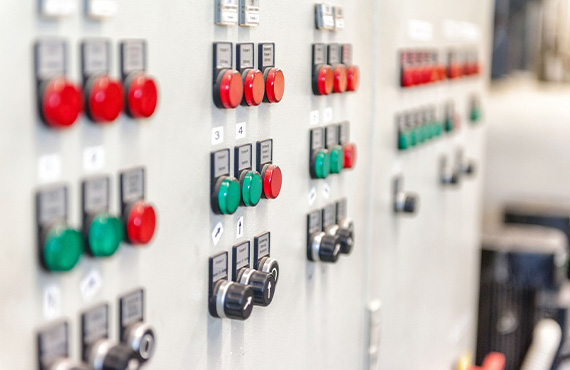
Safety and Compliance Considerations
Prioritizing quality in process automation control systems is crucial for ensuring the safety of personnel, protecting the environment, and meeting regulatory compliance standards. These systems often operate in high-risk environments, such as manufacturing plants, chemical processing facilities, or power generation sites, where even minor errors or malfunctions can have severe consequences.
Quality control systems play a vital role in mitigating risks by implementing robust safety measures and adhering to industry-specific regulations. They incorporate features like emergency shutdown procedures, fail-safe mechanisms, and real-time monitoring to detect and respond to potential hazards promptly. By maintaining strict quality standards, these systems minimize the likelihood of accidents, injuries, or environmental incidents.
Moreover, many industries are subject to stringent regulatory requirements imposed by government agencies or industry bodies. Quality automation systems are designed to comply with these regulations, ensuring that operations meet the necessary safety, environmental, and quality standards. Failure to comply can result in hefty fines, legal consequences, or even the suspension of operations.
Regular audits, certifications, and documentation processes are integral components of quality control systems, enabling organizations to demonstrate their commitment to safety and compliance. These systems also facilitate traceability, enabling manufacturers to track and recall products in the event of quality issues, minimizing the impact on consumers and the environment.
By prioritizing quality in process automation control systems, organizations can proactively address potential risks, safeguard their personnel and assets, and maintain a strong reputation for responsible and compliant operations.
Cost Savings and ROI
Investing in a high-quality process automation control system can lead to significant cost savings and improved return on investment (ROI) over the long term. While the upfront costs of implementing a robust and reliable system may be higher, the benefits it provides in terms of increased uptime, reduced maintenance requirements, and enhanced operational efficiency can quickly offset the initial investment.
High-quality automation systems are designed to minimize downtime and maximize productivity. By ensuring seamless operation and minimizing the risk of system failures or errors, businesses can maintain consistent output and avoid costly production disruptions. This increased uptime translates into higher throughput, improved customer satisfaction, and ultimately, increased revenue.
Also, well-designed and properly implemented automation systems require less frequent maintenance and repair. High-quality components and robust system architecture reduce the likelihood of breakdowns and malfunctions, resulting in lower maintenance costs. Additionally, these systems often incorporate advanced diagnostics and monitoring capabilities, enabling proactive maintenance and early detection of potential issues, further minimizing costly repairs and unplanned downtime.
Quality automation systems also contribute to improved energy efficiency and resource optimization. By optimizing processes and minimizing waste, businesses can reduce operational costs associated with energy consumption, raw material usage, and waste disposal. This not only contributes to cost savings but also aligns with sustainability goals and environmental responsibilities.
Ultimately, the investment in a high-quality process automation control system can provide a significant return on investment by reducing long-term operational costs, increasing productivity and efficiency, and minimizing downtime and disruptions. By prioritizing quality and reliability, businesses can achieve a competitive advantage, enhance profitability, and position themselves for long-term success in an increasingly automated and technology-driven industrial landscape.
Quality Assurance and Best Practices
Implementing robust quality assurance practices is crucial for ensuring the reliability, safety, and efficiency of process automation control systems. Adhering to industry standards, conducting rigorous testing, and following proven methodologies can help organizations mitigate risks, minimize downtime, and maximize the return on their automation investments.
One widely adopted methodology is the V-model, which provides a structured approach to system development and testing. This model emphasizes early validation and verification activities, such as requirements analysis, system design reviews, and component testing, before progressing to system integration and acceptance testing.
By following the V-model, you can identify and address potential issues early in the development lifecycle, reducing the cost and effort required for rework and bug fixes.
Another essential aspect of quality assurance is comprehensive testing. This includes unit testing, integration testing, system testing, and user acceptance testing. Automated testing tools and frameworks can streamline the testing process, enabling continuous integration and delivery pipelines. Additionally, techniques like fault injection testing and stress testing can help identify potential failure modes and assess system resilience under extreme conditions.
Adhering to industry standards and best practices, such as those outlined by organizations like the International Society of Automation (ISA) and the National Institute of Standards and Technology (NIST), can further enhance the quality and reliability of automation control systems. These standards provide guidelines for system design, development, deployment, and maintenance, ensuring consistency and interoperability across different components and systems.
Effective quality assurance also involves regular design reviews and audits. These activities bring together cross-functional teams, including engineers, subject matter experts, and stakeholders, to evaluate the system design, identify potential risks, and propose improvements. Design reviews can help catch issues early, reducing the likelihood of costly rework or system failures.
Finally, you should prioritize training and knowledge transfer to ensure that personnel responsible for operating and maintaining the automation control systems have the necessary skills and expertise. Comprehensive documentation, user manuals, and ongoing training programs can help facilitate a smooth transition and ensure consistent adherence to quality assurance practices throughout the system lifecycle.
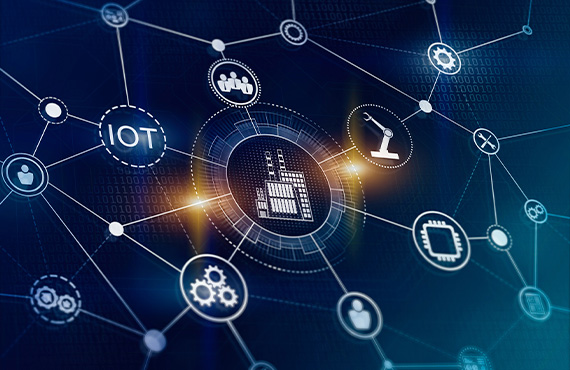
The Future of Quality Automation
The future of quality automation is being shaped by several emerging trends and innovations that aim to enhance the reliability, efficiency, and accuracy of process control systems. One of the most promising developments is the integration of artificial intelligence (AI) and machine learning (ML) technologies.
These technologies can analyze vast amounts of data from various sources, identify patterns, and make predictive decisions to optimize processes and detect potential issues before they occur.
The Industrial Internet of Things (IIoT) is another game-changer in the realm of quality automation. By connecting machines, sensors, and systems, IIoT enables real-time data collection and monitoring, allowing for proactive maintenance, predictive analytics, and seamless communication between different components of the automation system.
Digital twins, virtual representations of physical assets or processes, are also gaining traction in quality automation. These digital replicas can simulate various scenarios, test new configurations, and optimize processes without disrupting actual operations. This technology not only enhances quality but also facilitates training, troubleshooting, and efficient decision-making.
Advanced analytics tools, powered by big data and machine learning algorithms, are revolutionizing quality automation. These tools can analyze vast amounts of data from various sources, such as sensor readings, production logs, and quality control reports, to identify patterns, trends, and root causes of quality issues. This in-depth analysis enables data-driven decision-making, proactive quality control, and continuous process improvement.
As these technologies continue to evolve and become more accessible, the future of quality automation promises to be more intelligent, interconnected, and data-driven, leading to higher levels of precision, efficiency, and quality assurance in manufacturing and process control systems.