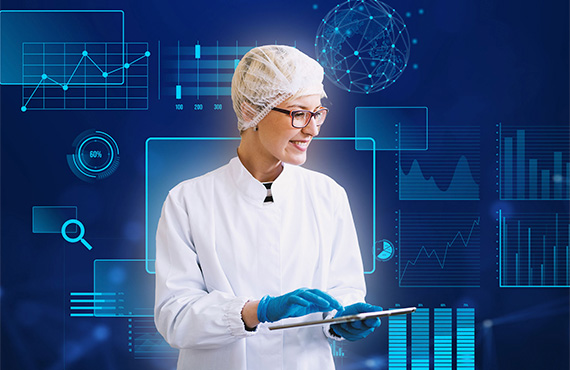
Did you know that businesses lose up to $260,000 per hour due to equipment downtime? In today's fast-paced industrial landscape, efficient maintenance management isn't just an option—it's a necessity for survival and growth.
Maintenance Management Software (MMS) or, Computerized Maintenance Management Software (CMMS), is changing the way you manage equipment maintenance, facility management, and asset upkeep throughout your organization. This digital solution turns traditional maintenance methods into efficient, data-driven processes that:
- Reduce unexpected breakdowns
- Extend equipment lifespan
- Cut operational costs
- Boost workplace safety
- Enhance team productivity
Your choice of maintenance management software can greatly impact your operational efficiency. The right system serves as the central nervous system of your organization, coordinating maintenance tasks, monitoring asset performance, and providing real-time insights for informed decision-making. As industries evolve and technology advances, selecting software that aligns with your specific needs becomes crucial for maintaining a competitive edge and ensuring sustainable growth.
Understanding Maintenance Management Software
MMS is your digital command center for managing asset maintenance operations. It replaces traditional maintenance practices with efficient, data-driven processes that improve operational efficiency.
Key Features of MMS:
- Work Order Management: Create, assign, and track maintenance tasks
- Asset Reliability: Monitor equipment performance and maintenance history
- Inventory Control: Manage spare parts and supplies
- Preventive Maintenance: Schedule regular maintenance activities
- Documentation: Store and access maintenance procedures and manuals
- Analytics: Generate reports and insights for decision-making
An MMS or CMMS takes these capabilities further by automating complex maintenance workflows. Your CMMS serves as a central hub, connecting maintenance teams, equipment data, and work processes in real-time.
Impact on Business Operations:
- Reduced equipment downtime through predictive maintenance
- Extended asset lifespan with regular maintenance scheduling
- Enhanced team productivity via mobile accessibility
- Improved compliance through automated documentation
- Cost savings from optimized inventory management
- Data-driven insights for refining maintenance strategy
Your maintenance software becomes a strategic asset by transforming raw data into actionable insights. It helps identify patterns in equipment performance, predict potential failures, and optimize maintenance schedules based on actual usage rather than fixed intervals.
The system's ability to track maintenance metrics provides clear visibility into your maintenance operations, enabling you to make informed decisions about resource allocation and equipment replacement.
Industry-Specific MMS Needs
Each industry has its own maintenance challenges that need specialized solutions. Your maintenance management software should match the specific needs of your industry for it to work effectively.
Your maintenance management software should address these unique requirements while providing flexibility for customization as your needs evolve. Consider software solutions that offer industry-specific modules designed to handle your sector's particular demands.
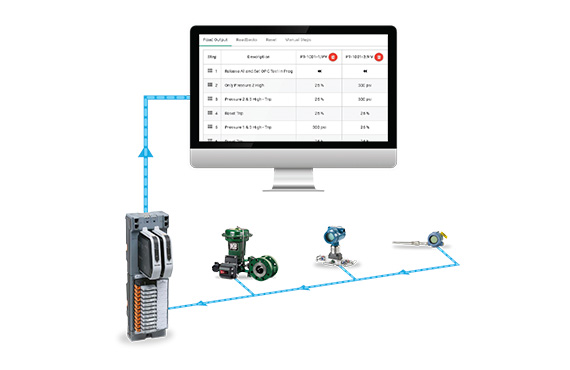
Key MMS Features to Keep in Mind
Your maintenance management software needs to include specific features that align with your operational requirements. Here's what you need to consider:
Essential Features for Every Industry
Data Validation: Automatic validation of manually entered and electronic data.
Collaborative Work Environment: Supports multiple users working on a single procedure, shortening duration and increasing visibility.
Offline Data Entry: Offers freedom of physical movement in and out of network communications.
User-Friendly Interface and App: Intuitive navigation system, clear menu structures, customizable workspace layouts, and quick-access tools for common tasks.
Mobile Accessibility: Real-time updates from any location, field technician support, offline functionality, and mobile-responsive design.
Reporting and Analytics: Custom dashboard creation, data visualization tools, automated report generation, and KPI tracking capabilities.
System Integration: API connectivity options, ERP system compatibility, IoT device integration, and third-party software synchronization.
Asset Management: Equipment lifecycle tracking, inventory control, spare parts management, and warranty information storage.
Next-Gen Workforce Attraction: Attract and retain the next generation of workers with digital processes and tools.
Industry-Specific Feature Requirements
Your software selection should prioritize features that address your specific pain points. Features that are essential for oil & gas may not be essential for pharmaceutical manufacturing. Consider scalability in your feature requirements - your chosen software should grow with your organization and adapt to changing industry demands.
Evaluating Your Options
Selecting the right maintenance management software requires a systematic approach. Here's your practical guide to evaluating CMMS solutions:
1. Assess Current Processes
- Document existing maintenance workflows
- Identify bottlenecks and inefficiencies
- List specific pain points your team faces
- Map out your ideal maintenance process
2. Create a Requirements Checklist
- Essential features needed for daily operations
- Industry-specific compliance requirements
- Integration needs with current systems
- Team size and user access requirements
- Budget constraints and ROI expectations
3. Research Available Solutions
- Create a shortlist of vendors specializing in your industry
- Compare feature sets against your requirements
- Check vendor reputation and market presence
- Verify customer support availability and quality
4. Gather Real-World Insights
- Read customer reviews on software review platforms
- Study case studies from similar businesses
- Connect with industry peers using CMMS solutions
- Join relevant online forums and communities
5. Test Drive Your Options
- Request personalized product demonstrations
- Sign up for free trials when available
- Test the software with real maintenance scenarios
- Involve key team members in the evaluation process
- Document user experiences and feedback
Pro Tips for Software Evaluation:
- Time your trials during typical operational periods
- Test mobile functionality in actual work environments
- Verify data migration capabilities
- Check customization options with vendor support
- Evaluate the learning curve for your team
Budget Considerations for Your MMS
Understanding the financial implications of maintenance management software implementation helps you make an informed investment decision. Here's what you need to consider:
Initial Setup Costs
- Software licensing fees
- Hardware requirements
- Staff training expenses
- Data migration costs
- System configuration and customization
Subscription Models vs. One-Time Purchases
- Software as a Service (SaaS): Monthly/annual subscription with automatic updates
- Perpetual License: Single upfront payment with optional maintenance fees
- Hybrid Models: Combination of upfront costs and recurring fees
ROI Calculation Factors
- Reduced equipment downtime
- Lower maintenance labor costs
- Extended asset lifespan
- Decreased inventory carrying costs
- Improved work order completion rates
Hidden Cost Considerations
- System upgrades
- Additional user licenses
- Technical support fees
- Custom integration expenses
- Data storage requirements
To calculate your potential ROI, track these metrics:
- Average repair time reduction
- Preventive maintenance completion rates
- Asset failure frequency
- Labor productivity improvements
- Spare parts optimization
A comprehensive maintenance management system typically delivers ROI within 12-18 months through reduced operational costs and enhanced efficiency. Your industry-specific requirements and organizational size will influence the total investment needed for successful implementation.
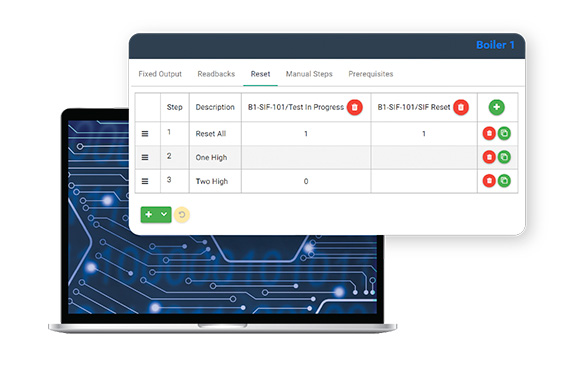
Explore Our Maintenance Management Software Solutions
Ready to transform your maintenance operations? We offer industry-leading maintenance management software solutions, such as ProofCheck™, QuickView+™, and AlertTrack SNAP-ON software, designed to meet your specific needs.
Our Solutions at Proconex Include:
- Industry-Specific Packages - Tailored solutions for manufacturing, oil & gas, power generation, and much more
- Flexible Implementation Options - Cloud-based and on-premises solutions to match your infrastructure
- Comprehensive Training - Expert-led sessions to ensure your team maximizes software benefits
- 24/7 Technical Support - Dedicated assistance whenever you need it
Get Started Today:
- Schedule a free consultation with our experts
- Receive a customized demo of our software
- Experience our risk-free trial period
Why Choose Proconex?
- 75+ years of experience
- Proven track record of success across multiple industries
- Regular updates and feature enhancements
- Seamless integration with existing systems
- Scalable options for businesses of all sizes
Contact Us:
Book your free consultation now and discover how our maintenance management system software can revolutionize your operations. Our team of experts is ready to help you find the perfect solution for your industry-specific needs.