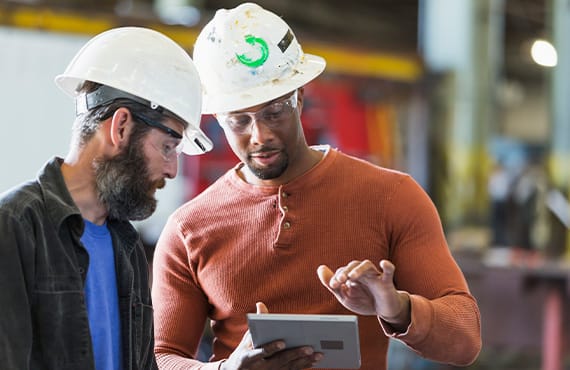
Power generation systems are essential for modern industrial facilities, and their reliability is crucial for uninterrupted, consistent functioning.
Asset reliability monitoring plays a vital role in ensuring the smooth operation of these complex systems by providing valuable insights that can prevent costly shutdowns. Your power generation infrastructure faces constant challenges:
- Equipment wear-and-tear
- Unexpected system failures
- Performance inefficiencies
- Increasing maintenance costs
Advanced asset monitoring solutions turn these challenges into opportunities for improvement. By using advanced monitoring systems, you can gain real-time visibility into the health and performance of your equipment.
With remote monitoring capabilities and data analysis, you can now:
- Identify potential problems before they become major issues
- Optimize maintenance schedules based on the actual condition of your equipment
- Minimize unplanned downtime through proactive measures
- Extend the lifespan of your assets with informed decision-making
This comprehensive guide explores how modern asset monitoring solutions enhance operational efficiency and system reliability in power generation facilities. You'll discover practical ways to use these technologies to maximize your system's performance while reducing operational risks.
Understanding Asset Monitoring Solutions
Asset monitoring in power generation systems is a complete way of keeping track of important equipment performance. It involves using hardware sensors, software solutions, and analytical tools to get real-time information about how assets are doing and how efficiently they are operating.
Key Components of Asset Monitoring Systems:
Sensor Networks: Advanced sensors measure vital parameters including:
- Temperature variations
- Vibration levels
- Pressure readings
- Oil condition
- Electrical performance
Data Collection Systems: Automated systems gather and store operational data from multiple sources across the facility
Analysis Platforms: Sophisticated software interprets collected data to identify patterns and potential issues
Traditional vs Advanced Monitoring Methods:
Traditional Methods Advanced Technologies Manual equipment inspections
- Real-time remote monitoring capabilities
- Scheduled maintenance routines
- AI-powered predictive analytics
- Basic performance logging
- Wireless sensor networks
- Periodic testing procedures
- Cloud-based data management
- Digital twin technology
These asset monitoring solutions have changed the way facilities take care of their assets. Instead of waiting for something to go wrong and then fixing it (reactive maintenance), they can now actively manage their assets and prevent problems before they happen (proactive asset management).
With over 75 years of experience, Proconex implements these solutions across various industries, integrating Emerson's cutting-edge automation technologies with customized monitoring strategies for power generation systems.
The combination of these monitoring solutions creates a strong system for keeping the power generation process reliable while also making it more efficient. This all-encompassing method allows power generation systems to consistently perform at their best by regularly checking and finding problems early on.
The Role of Remote Asset Monitoring in Enhancing Reliability
Remote asset reliability monitoring transforms power generation system maintenance through real-time insights and continuous surveillance. This technology enables operators to track critical equipment performance 24/7, identifying potential issues before they escalate into costly failures.
Key Benefits of Remote Monitoring:
- Instant alerts for equipment anomalies
- Reduced need for physical inspections
- Enhanced safety through remote diagnostics
- Optimized resource allocation
- Improved decision-making capabilities
These systems integrate seamlessly with existing infrastructure, providing plant operators with comprehensive dashboards and automated reporting capabilities for operations analytics. The technology adapts to various facility sizes, from large power plants to smaller commercial enterprises.
Advanced algorithms analyze equipment behavior patterns, creating baseline performance metrics and identifying deviations that require attention. This proactive approach enables maintenance teams to address issues during planned maintenance windows, maximizing system uptime and operational efficiency.
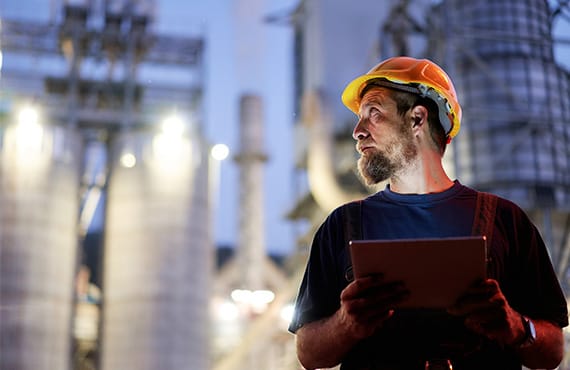
Using Operations Analytics for Proactive Maintenance Strategies
Operations analytics, like our proprietary operations analytics software system, DataJaguar™, turns raw asset monitoring data into actionable insights, allowing you to predict and prevent equipment failures before they happen. By examining past performance data, real-time sensor readings, and equipment behavior patterns, you can implement targeted maintenance strategies that maximize system reliability.
Key Benefits of Data-Driven Maintenance:
- Identify subtle performance degradation patterns
- Detect anomalies in equipment behavior
- Optimize maintenance scheduling
- Reduce unnecessary maintenance activities
- Extend equipment lifespan
A power generation facility in Pennsylvania used data analytics to monitor their turbine systems. The analysis uncovered small changes in vibration patterns that traditional monitoring methods overlooked. This early detection prevented a potential bearing failure, saving an estimated $2.5 million in repairs and downtime costs.
How Data Analytics Can Help Your Maintenance Strategy
- Pattern Recognition: Advanced algorithms identify subtle changes in equipment performance that may indicate developing issues
- Predictive Modeling: Machine learning models predict potential failures based on historical data
- Real-time Analysis: Continuous monitoring allows for immediate response to emerging problems
- Performance Optimization: Data-driven insights help fine-tune equipment settings for maximum efficiency
Your maintenance teams can use these insights to schedule repairs during planned outages, reducing unexpected downtime. For instance, a chemical processing plant used predictive analytics to extend their maintenance intervals by 40%, while simultaneously decreasing emergency repairs by 75%.
By combining asset condition monitoring with advanced data analytics, you create a powerful system that shifts maintenance from reactive to proactive. This method helps you maintain optimal equipment performance while minimizing operational disruptions.
Managing Complexity: Ensuring System Harmony with Effective Condition Monitoring
Modern power generation systems are complex networks of various technologies working together. Each part, whether it's a traditional turbine or a renewable energy component, must function smoothly within the larger system.
A Typical Power Plant Setup
Here's an overview of a typical power plant setup:
1. Multiple Generation Sources
- Gas turbines
- Steam generators
- Solar arrays
- Wind turbines
2. Supporting Infrastructure
- Control systems
- Cooling systems
- Power distribution networks
- Safety mechanisms
Effective condition monitoring serves as the conductor of this technological orchestra. Advanced monitoring systems track the performance metrics of each component while analyzing their interactions with other systems. This comprehensive approach helps identify potential conflicts before they affect operations.
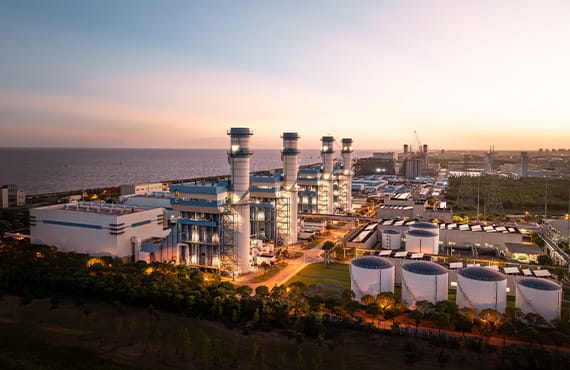
The Benefits of Real-Time Monitoring
Real-time monitoring enables:
- Synchronized operation between different power generation units
- Balanced load distribution across systems
- Early detection of compatibility issues
Optimal Resource Allocation
A practical example is the integration of renewable sources with conventional power generation. Condition monitoring systems help manage the variable nature of renewable inputs while maintaining stable power output. These systems continuously adjust parameters across all components to ensure harmonious operation.
The key to managing this complexity lies in implementing monitoring solutions that can adapt to evolving technology landscapes while maintaining system stability and reliability.
Overcoming Challenges in Implementing Asset Monitoring Solutions
Implementing asset monitoring solutions in power generation systems presents several key challenges that organizations must address:
1. Data Security Concerns
- Protecting sensitive operational data from cyber threats
- Ensuring compliance with industry regulations
- Maintaining secure remote access protocols
- Implementing robust authentication systems
2. Staff Resistance to Change
- Fear of job displacement
- Unfamiliarity with new technologies
- Concerns about increased workload
- Reluctance to modify established procedures
3. Effective Implementation Strategies
Stakeholder Engagement
- Involve key personnel from the planning phase
- Create cross-functional implementation teams
- Establish clear communication channels
- Set realistic expectations and timelines
Comprehensive Training Programs
- Develop role-specific training modules
- Provide hands-on experience with new systems
- Offer ongoing technical support
- Create documentation and reference materials
Change Management Approach
- Demonstrate tangible benefits to staff
- Address concerns proactively
- Celebrate early wins and successes
Foster a Culture of Continuous Improvement
At Proconex, our deep dedication to our employees and customers drives us to prioritize thorough training and support during system implementations. We understand that successful asset monitoring integration requires both technical expertise and strong change management strategies.
The Future of Asset Monitoring in Power Generation Systems
The asset monitoring landscape is rapidly evolving with groundbreaking technologies reshaping power generation reliability. AI-powered predictive analytics and machine learning algorithms are becoming increasingly sophisticated, enabling unprecedented accuracy in fault detection and performance optimization.
Emerging trends to watch:
- Digital twin technology creating virtual replicas of physical assets
- 5G connectivity enabling real-time monitoring across vast networks
- Edge computing bringing faster processing capabilities to remote locations
- IoT sensors providing deeper insights into asset health
The power generation industry stands at a technological crossroads. Organizations that embrace these advanced monitoring solutions will gain a significant competitive advantage through improved reliability, reduced costs, and enhanced operational efficiency.
Ready to transform your power generation system's reliability?
Contact Proconex today to discover how our cutting-edge asset monitoring solutions can transform your operations. With our 75+ years of industry expertise and partnership with Emerson Automation Solutions, we'll help you implement the right monitoring strategy for your specific needs.