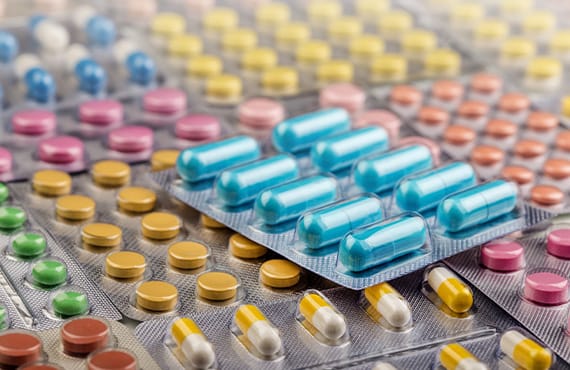
Batch processing is a crucial part of modern industrial manufacturing. It involves producing goods in large quantities, or "batches," rather than individually. This method allows for precise quality control and consistent products in important industries.
How Does Batch Processing Work?
At the core of batch processing are complex process control systems that manage the production. These systems are designed to handle specific amounts of materials and maintain controlled conditions throughout the operation.
Key Elements of Batch Processing:
- Materials - The raw ingredients or components used in the production process.
- Controlled Conditions - The specific environment in which the manufacturing takes place, including factors like temperature, pressure, and humidity.
- Variables - The different aspects of the process that can be adjusted or monitored, such as mixing speeds, reaction times, and ingredient proportions.
Key Industries Benefiting from Batch Processing
- Life Sciences/Pharmaceutical Manufacturing: Batch processing allows for strict control over the strength and purity of medications, which is vital for patient safety and meeting regulations.
- Chemical Production: Chemical manufacturers use batch systems to ensure exact mixtures and reaction conditions, guaranteeing reliable products.
- Food and Beverage Industry: The food and beverage sector uses batch processing to maintain consistent flavors while adhering to strict safety standards.
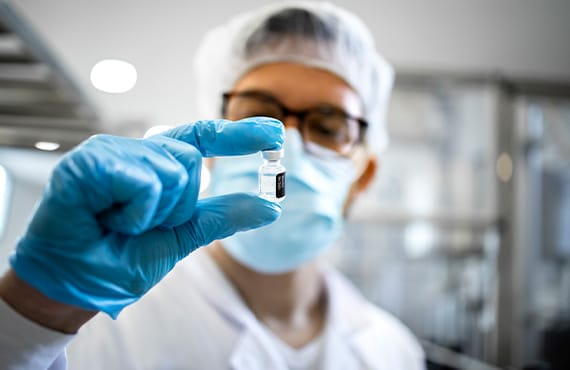
The Components of Batch Processing
A successful batch processing system relies on two main elements:
- Recipe Management Systems
- Equipment Control Integration
What Are Recipe Management Systems?
These systems are responsible for managing the production recipes or formulas used in batch processing. They ensure that each batch is produced according to predefined specifications and parameters. Some key features of recipe management systems include:
- Digital recipe libraries storing precise production parameters
- Automated ingredient calculations and scaling capabilities
- Real-time monitoring of recipe execution
- Historical data tracking for quality assurance
Equipment Control Integration
In addition to managing recipes, batch processing also requires coordination between different pieces of equipment involved in the production process. This integration ensures that all machines work together seamlessly to achieve optimal results. Important aspects of equipment control integration include:
- Synchronized operation of mixers, reactors, and vessels
- Automated valve sequencing and flow control
- Temperature and pressure regulation
- Safety interlocks and emergency protocols
What Are the Benefits of Batch Processing?
Implementing batch processing in manufacturing operations offers several advantages:
- Quality Assurance Benefits
- Consistent product specifications across batches
- Reduced human error through automation
- Complete batch documentation and traceability
- Early detection of process deviations
- Operational Efficiency Gains
- Optimized resource utilization
- Reduced material waste
- Lower production costs
- Improved equipment maintenance scheduling
Modern Advancements in Batch Processing
With advancements in technology, modern batch processing systems have become even more sophisticated. They now incorporate features like real-time analytics and predictive maintenance capabilities.
These technologies enable manufacturers to:
- Maintain precise control over their production processes
- Adapt to changing market demands
- Meet regulatory requirements
How Technology is Transforming Batch Processing
Traditional batch processing methods have been transformed by advanced automation solutions:
- DataJaguar software enables real-time monitoring and analysis of processes
- VisionAI technology automates quality inspections and identifies defects
- Integrated process control and safety systems ensure consistency from one batch to another
- Digital transformation tools allow for complete tracking of production
These technological advancements give manufacturers the ability to achieve unmatched levels of quality control, efficiency, and consistency in their batch operations. The outcome: superior products that meet precise specifications while upholding the highest safety standards.
The Role of Standardization in Batch Processing
One key aspect of batch processing is its emphasis on standardization. By creating a consistent production environment where each batch follows identical procedures under carefully controlled conditions, manufacturers can ensure product consistency. In industries like pharmaceutical manufacturing, it is essential to be consistent with a product. The last thing a consumer should experience, for example, is one Advil pill being 10x the strength of another one in the same bottle!
However, it's also important to note that flexibility is still possible within this framework. When necessary, parameters can be adjusted or modified to accommodate specific needs or preferences. This combination of standardization and flexibility makes batch processing an effective solution for industries requiring both uniformity and adaptability in their manufacturing processes.
Ensuring Quality in Pharmaceuticals with Batch Processing
Pharmaceutical manufacturing requires uncompromising precision in every production step. A single mistake can affect the effectiveness of the drug, the safety of the patient, and compliance with regulations. Batch processing is essential for ensuring quality control in pharmaceuticals, allowing manufacturers to:
- Maintain consistent potency across production runs
- Monitor and record each stage of manufacturing
- Conduct quality checks in real-time
- Keep batches separate to avoid contamination
Meeting FDA Regulations with Batch Processing
The FDA requires pharmaceutical companies to prove that their products are consistently high-quality by using validated processes. Batch processing systems provide detailed records of:
- Specifications for raw materials
- Parameters for production
- Conditions of equipment
- Controls for the environment
- Results of quality tests
These records help manufacturers to:
- Identify issues early in the production cycle
- Isolate suspicious batches before they are distributed
- Trace the history of a product for regulatory audits
- Verify cleaning procedures between batches
The Importance of Rigorous Testing in Pharmaceuticals
The strict requirements for purity and potency in the pharmaceutical industry make batch processing essential. Each batch goes through thorough testing protocols to ensure that medications meet precise standards before they are released. This systematic approach prioritizes patient safety and ensures compliance with the FDA's Current Good Manufacturing Practice (CGMP) guidelines.
Achieving Consistent Product Composition in Chemicals through Batch Processing
Chemical manufacturing has its own set of challenges that require careful control and monitoring. Even a small change in reaction conditions can result in significant differences in product quality and safety.
Key Challenges in Chemical Manufacturing:
- Temperature fluctuations affecting reaction rates
- Pressure variations impacting yield
- pH level maintenance for optimal reactions
- Raw material consistency
- Cross-contamination risks
Batch processing systems tackle these challenges by implementing strict control methods. Each batch is treated as an independent unit, which allows for:
- Real-time monitoring of critical parameters
- Automated adjustments to maintain optimal conditions
- Complete documentation of process variables
- Isolation of potential quality issues
Advanced solutions like DataJaguar software empower manufacturers to monitor every aspect of the production process. This powerful tool offers:
- Detailed batch genealogy
- Parameter trending analysis
- Quality control documentation
- Deviation alerts
VisionAI technology takes batch processing to the next level by:
- Detecting anomalies in real-time
- Predicting maintenance needs
- Optimizing reaction conditions
- Reducing waste and rework
These technological advancements create a controlled environment where chemical reactions occur under ideal circumstances. The outcome: consistent product composition, batch after batch. Quality control measures guarantee that each batch meets precise requirements, while safety protocols safeguard both products and personnel.
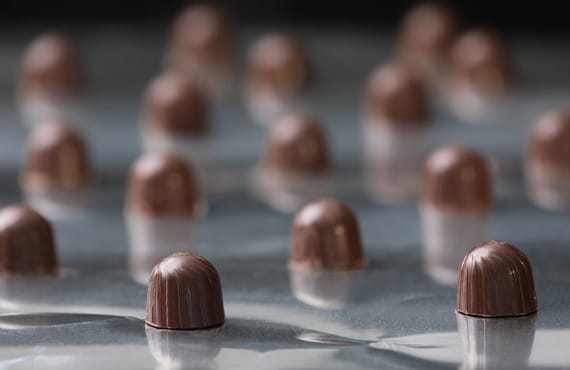
Maintaining Flavor Profiles and Food Safety Standards in Food & Beverage Production Using Batch Processing Techniques
The food and beverage industry faces unique challenges in maintaining consistent flavor profiles while adhering to strict safety standards. Temperature-sensitive ingredients and complex recipe formulations require precise control throughout the production process.
Key Temperature-Related Challenges:
- Raw material degradation at incorrect storage temperatures
- Flavor compound volatility during processing
- Microbial growth risk zones
- Product texture variations due to temperature fluctuations
Batch processing systems equipped with advanced monitoring capabilities help manufacturers maintain strict control over these critical parameters. Proconex's DataJaguar software provides real-time tracking of temperature zones, processing times, and ingredient additions, ensuring each batch meets exact specifications.
Quality Control Through Advanced Technology:
- VisionAI solutions detect product inconsistencies through visual inspection
- Automated recipe management prevents formula deviations
- Real-time process monitoring maintains optimal conditions
- Digital record-keeping ensures traceability
Food safety compliance requires documented evidence of proper handling procedures. Batch processing systems create detailed records of:
- Temperature logs throughout production
- Ingredient addition sequences
- Equipment cleaning cycles
- Quality check results
- Batch genealogy
These automated systems significantly reduce human error while increasing production efficiency. The integration of DataJaguar and VisionAI technologies enables manufacturers to maintain consistent flavor profiles across multiple production runs while meeting stringent food safety requirements.
The Role of Automation and Digital Transformation in Enhancing Batch Processing Efficiency
Digital transformation is changing the game for batch processing by introducing advanced automation solutions. Proconex is at the forefront of this revolution, offering state-of-the-art automation technologies that make manufacturing operations smoother and more efficient.
Key automation capabilities include:
- Real-time process monitoring and control
- Predictive maintenance algorithms
- Automated recipe management
- Data analytics for process optimization
- Remote monitoring capabilities
Emerson's DeltaV™ Batch software enables manufacturers to implement flexible batch strategies while maintaining strict quality controls. This advanced system allows you to:
- Configure and modify recipes without production interruption
- Track batch genealogy and maintain detailed electronic records
- Integrate seamlessly with existing manufacturing systems
- Scale production up or down based on demand
These automation solutions reduce human error, increase production speed, and ensure consistent product quality. Modern batch automation systems also provide detailed analytics, helping you identify bottlenecks and optimize production cycles for maximum efficiency.
In Conclusion: Embracing the Future of Batch Processing through Advanced Technologies
The future of batch processing software points toward intelligent, self-optimizing systems powered by artificial intelligence and machine learning. These technologies enable:
- Predictive Analytics: Systems that anticipate equipment failures and quality deviations before they occur
- Digital Twins: Virtual replicas of physical processes for real-time monitoring and optimization
- Edge Computing: Faster processing and reduced latency in batch operations
- Cloud Integration: Enhanced data accessibility and remote monitoring capabilities
The industrial manufacturing landscape continues to evolve with IoT-enabled sensors and advanced data analytics. These innovations drive:
- Real-time quality control adjustments
- Automated recipe modifications based on environmental conditions
- Enhanced traceability and compliance reporting
- Improved resource allocation and energy efficiency
You can position your manufacturing operations for success by implementing these advanced technologies. Proconex offers cutting-edge solutions that align with these emerging trends, helping you achieve higher production efficiency and maintain competitive advantage in your industry.
FAQs about Batch Processing in Industrial Manufacturing Industries
Batch processing is a manufacturing method where materials are produced in discrete groups rather than continuous flows. This systematic approach enables precise control over production parameters, ensuring each batch meets specific quality standards before moving to the next stage.
Batch processing creates controlled environments with:
- Precise measurement of ingredients
- Standardized processing conditions
- Real-time monitoring of critical parameters
- Documentation of each production step
- Quality checks between stages
Three key industries rely heavily on batch processing:
- Pharmaceuticals: Maintains uniform potency and meets FDA compliance
- Chemicals: Controls reaction parameters for consistent composition
- Food & Beverage: Ensures flavor consistency and food safety standards
Modern automation solutions deliver:
- Reduced human error through automated workflows
- Enhanced traceability with digital record-keeping
- Improved efficiency via DataJaguar software integration
- Advanced quality control using VisionAI technology
- Real-time process optimization
As an exclusive Emerson Impact Partner, Proconex delivers:
- Comprehensive automation solutions
- Advanced process control systems
- Cutting-edge software integration
- Expert technical support
- Industry-specific customization
These solutions help manufacturers achieve higher quality standards while reducing operational costs through efficient batch processing systems.