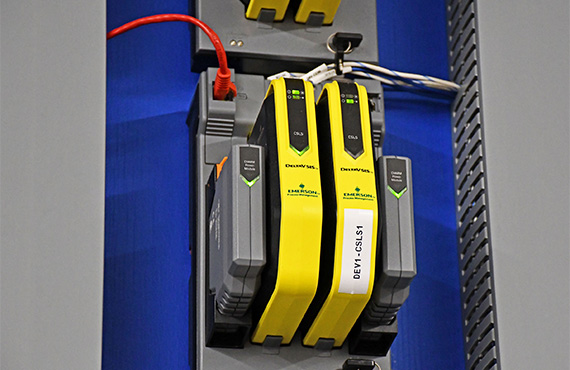
Industrial processes have become complex systems where one malfunction can lead to disastrous outcomes. Manufacturing facilities now face significant challenges in maintaining safety standards while handling intricate process control operations.
A Safety Instrumented System (SIS), such as Emerson’s DeltaV, is critical in preventing potential disasters in modern industrial facilities. These specialized systems:
- Monitor process conditions continuously
- Automatically detect dangerous deviations
- Initiate immediate protective actions
- Prevent catastrophic failures
Safety Risks in Modern Industrial Environments
Modern industrial facilities come with considerable dangers, such as:
- Chemical releases
- Equipment failures
- Process deviations
- Human errors
A well-designed SIS serves as a guardian for your facility, ready to step in when regular control systems fall short. These systems provide an independent layer of protection, functioning separately from basic process control to guarantee maximum safety.
In this guide, you'll learn about:
- Key components of SIS and their roles
- Importance of SIS in managing process safety
- Regulatory compliance obligations
- Advantages of implementing SIS
- Upcoming technological advancements
Understanding the significance of SIS is the first step in safeguarding lives, assets, and the environment in today's demanding industrial world.
What is a Safety Instrumented System?
According to the NIST, an SIS is a system that is composed of sensors, logic solvers, and final control elements whose purpose is to take the process to a safe state when predetermined conditions are violated. Other terms commonly used include emergency shutdown system (ESS), safety shutdown system (SSD), and safety interlock system (SIS). Unlike Basic Process Control Systems (BPCS), which manage normal operations, SIS has a specific focus on safety.
Core Components of SIS:
- Sensors/Transmitters: These devices monitor important variables in the process, such as temperature, pressure, and flow rates.
- Logic Solvers: The logic solvers receive input signals from the sensors and execute pre-programmed safety logic based on those signals.
- Final Elements: Actuators and valves are the final components that carry out the safety actions determined by the logic solvers.
SIS systems have several key differences compared to traditional BPCS:
- Primary Focus: While BPCS is responsible for managing routine operations, SIS prioritizes safety and preventing hazards.
- Independence: SIS operates separately from BPCS to ensure that any issues with the control system do not affect its safety functions.
- Design Philosophy: SIS follows fail-safe design principles and incorporates redundancy to enhance reliability.
- Testing Requirements: Regular proof-testing is conducted to validate the performance of SIS, whereas BPCS maintenance schedules may not have the same level of scrutiny.
Plant operators interact with both systems in different ways. BPCS requires active control and adjustments from operators, while SIS remains inactive until safety parameters are violated. This separation ensures that production pressures never compromise critical safety functions.
The complexity of modern industrial processes requires advanced safety measures. SIS systems offer this protection through a combination of dependable hardware, intelligent logic, and automated response capabilities.
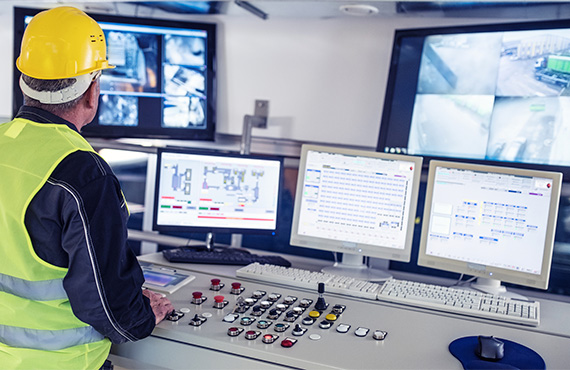
The Role of SIS in Preventing Hazardous Events
SIS are automated safety systems used in high-risk industrial environments to protect against hazardous events. These systems continuously monitor critical process parameters and take immediate actions to prevent dangerous situations.
How a Safety Instrumented System Works: Automatic Safety Response Mechanisms
SIS has built-in mechanisms that automatically respond to specific unsafe conditions. Here are some examples:
- Shutdown valves activation during pressure spikes: When there is a sudden increase in pressure, the SIS will automatically close the valves to prevent any further escalation.
- Emergency venting during temperature excursions: If the temperature goes beyond the safe limits, the SIS will activate emergency venting to release excess heat and bring it back to normal levels.
- Equipment isolation during toxic gas detection: In case of detecting toxic gas leakage, the SIS will isolate the affected equipment to contain the hazard and protect personnel.
- Process flow interruption during critical deviations: If there are significant deviations from normal operating conditions, the SIS will interrupt the process flow to avoid potential accidents.
These safety measures are designed to work independently from regular control systems. While control systems focus on maintaining production efficiency, SIS prioritizes safety above all else.
Real-World Applications Across Industries
SIS has proven its effectiveness in various industries by successfully preventing catastrophic events. Here are some examples of how different sectors utilize these systems:
Oil & Gas Sector
- Automatic wellhead shutdown during pressure anomalies
- Emergency isolation of processing units
- Gas detection and ventilation control
- Pipeline pressure monitoring and protection
Chemical Manufacturing
- Reactor temperature control and emergency cooling
- Toxic gas containment systems
- Batch process safety interlocks
- Storage tank overfill prevention
Life Sciences Production
-
Sterile environment maintenance
- Critical temperature control for sensitive processes
- Containment systems for hazardous materials
- Precise pressure control in reaction vessels
The Importance of SIS Readiness
Your SIS system is always ready to act when needed. It constantly monitors safety parameters and can intervene within milliseconds if any breaches occur. This rapid response capability is crucial in preventing accidents and minimizing potential damages.
For instance, in the chemical industry, reactor safety systems powered by SIS have avoided runaway reactions that could lead to explosions or toxic releases. Similarly, oil refineries rely on these systems to manage emergency shutdowns of processing units, ensuring swift action during critical situations.
In pharmaceutical facilities where product quality and worker safety are paramount, SIS plays a vital role in maintaining strict environmental controls. By continuously monitoring factors such as temperature and pressure, these systems help uphold regulatory compliance while safeguarding sensitive processes.
By implementing robust Safety Instrumented Systems tailored to specific industry needs, organizations can significantly reduce risks associated with hazardous events.
Regulatory Compliance and Industry Standards for Safety Instrumented Systems
Safety Instrumented Systems require strict adherence to international standards and regulations to ensure optimal performance and reliability. Two primary standards govern SIS implementation:
1. IEC 61508
This standard establishes requirements for electrical, electronic, and programmable electronic safety systems. It defines safety integrity levels (SIL) and risk assessment methodologies, provides a framework for managing the entire safety lifecycle, and sets guidelines for verifying hardware and software.
2. IEC 61511
This is an industry-specific adaptation of IEC 61508 for process industries. It outlines requirements for specifying, designing, installing, and operating safety systems, defines validation and maintenance procedures, and establishes documentation requirements for various phases of the safety lifecycle.
Compliance with these standards delivers significant protective benefits:
Legal Protection
- Documentation of safety measures
- Proof of due diligence
- Reduced liability exposure
- Regulatory audit readiness
Financial Security
- Prevention of costly accidents
- Lower insurance premiums
- Reduced risk of regulatory fines
- Protection against production losses
Organizations must maintain detailed records of:
- Risk assessments
- Design specifications
- Testing procedures
- Maintenance activities
- Personnel training
- System modifications
Regular audits and assessments help ensure continued compliance and identify areas for improvement in your safety instrumented systems.
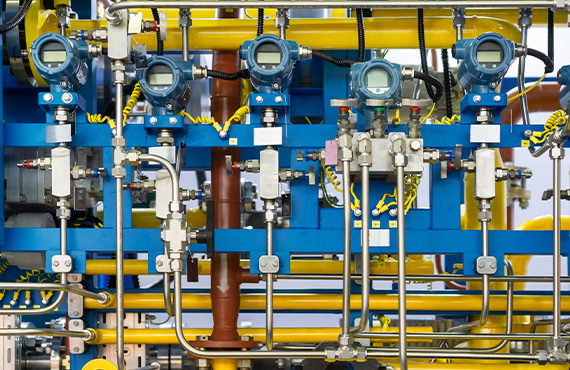
Benefits and Future Trends of Implementing Safety Instrumented Systems
Implementing Safety Instrumented Systems (SIS) delivers substantial advantages for your process control operations. Here's how SIS creates value for your organization:
Key Benefits
- Enhanced Safety Performance: SIS reduces workplace incidents by up to 80% through automated hazard detection and response
- Minimized Downtime: Intelligent monitoring prevents unexpected shutdowns, maintaining production continuity
- Improved Equipment Reliability: Proactive maintenance alerts help extend machinery lifespan
- Streamlined Compliance: Automated documentation and reporting simplify regulatory requirements
Cost-Saving Impacts
- Accident prevention saves $3-7 million per avoided incident
- Reduced insurance premiums through demonstrated safety measures
- Lower maintenance costs through predictive diagnostics
- Decreased operational disruptions and production losses
- Emerging Technologies Reshaping SIS
AI Integration
- Machine learning algorithms predict potential failures
- Pattern recognition improves hazard detection accuracy
- Automated decision-making speeds up response times
IoT Capabilities
- Real-time data collection from multiple sensors
- Remote monitoring and control capabilities
- Seamless integration with existing control systems
- Advanced analytics for performance optimization
Smart Sensors
- Self-diagnostic capabilities
- Wireless connectivity options
- Enhanced accuracy and reliability
- Reduced installation and maintenance costs
These technological advancements create smarter, more responsive safety systems that protect both your assets and workforce while driving operational excellence.
Proconex's Role in Enhancing Process Control Safety Measures Through SIS Solutions
Proconex is a leader in implementing safety instrumented systems (SIS), providing customized solutions that meet the specific needs of your industry. Our team of certified experts has decades of experience in designing, implementing, and maintaining SIS solutions across various industrial sectors.
Key Capabilities:
- Custom SIS design and integration
- Compliance verification with IEC standards
- Regular system maintenance and updates
- 24/7 technical support
- Training programs for your personnel
Your facility's safety requires a partner who understands the complexities of modern process control systems. At Proconex, we help you identify potential risks and implement effective SIS solutions that safeguard your assets, personnel, and operations.
Explore Our Safety Instrumented System Solutions!
Ready to enhance your safety measures?
Contact our team today for a comprehensive safety assessment and discover how our SIS solutions can strengthen your facility's safety protocols.