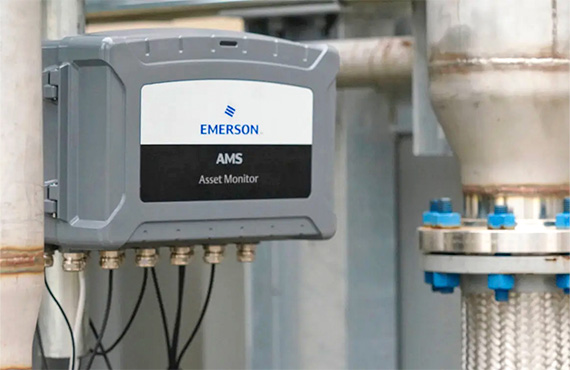
In today’s industrial landscape, keeping machines running smoothly isn’t just a goal; it’s a requirement. Downtime costs money, and unexpected failures can derail even the best operations.
That’s where wireless vibration sensors come in. These compact, powerful devices deliver real-time insights into machine health, catching issues before they spiral. At Proconex, we see firsthand how this technology transforms machine monitoring into a proactive powerhouse. Let’s explore why wireless vibration sensors are the ultimate tool for your machine health monitoring system.
What Are Wireless Vibration Sensors?
Wireless vibration sensors measure a machine’s vibrations; tiny shakes that signal wear, imbalance, or impending failure. Unlike wired setups, they don’t tether you to cables or complex installations. They stick onto equipment, collect data, and beam it straight to your dashboard via wireless networks.
The payoff is big. A MarketsandMarkets report pegs the vibration monitoring market at $2.5 billion by 2028, growing 7 percent yearly. Why? Industries crave real-time data to dodge downtime; and wireless vibration sensors deliver it fast.
Why Wireless Vibration Sensors Matter
Machine health monitoring isn’t new, but wireless tech takes it to the next level. Traditional wired sensors work fine; until you factor in installation headaches, maintenance hassles, and limited reach. Wireless vibration sensors are easy to deploy, scalable, and tough enough for harsh environments. At Proconex, we’ve watched clients swap clunky systems for these sleek solutions and never look back.
Stats back the hype. The International Society of Automation says predictive maintenance fueled by tools like vibration wireless sensors; cuts downtime by 30–50 percent. That’s not just uptime; it’s profit. Add in a 20 percent drop in maintenance costs, per Plant Engineering, and you’ve got a compelling case for going wireless.
Top Benefits of Wireless Vibration Sensors
Here’s why wireless vibration sensors shine in machine monitoring:
- Real-Time Insights: These devices track vibrations 24x7, sending alerts the moment something’s off. No lag, no guesswork; just data you can act on.
- Easy Setup: Stick them on, connect them up, and you’re rolling. No rewiring or shutdowns needed. Emerson, a leader in this space, highlights this perk: https://www.emerson.com/en-us/automation/measurement-instrumentation/vibration-monitoring.
- Cost Savings: Fewer cables, less labor. A Frost & Sullivan study notes wireless systems slash installation costs by 25–40 percent vs. wired setups.
- Scalability: Need to monitor 10 machines; or 100? Wireless vibration sensors grow with you, no overhaul required.
- Rugged Design: Built for dust, heat, and grime, they thrive where wired sensors falter; like in refineries or power plants.
Real-world wins seal the deal. A chemical plant using wireless vibration sensors caught a pump imbalance early, avoiding a $100,000 failure. That’s the kind of edge a machine health monitoring system delivers.
How They Transform Machine Monitoring
Machine health isn’t static; it’s a living pulse. Wireless vibration sensors keep tabs on that pulse, spotting trends like misalignment, bearing wear, or cavitation. They don’t just react; they predict. This shift from “fix it when it breaks” to “stop it before it does” is huge. The American Society of Mechanical Engineers reports that predictive maintenance boosts equipment life by 20–40 percent. That’s years added to your assets.
Take a power generation facility. They rigged turbines with vibration wireless sensors and saw uptime jump 35 percent. Why? Real-time data flagged issues; like excessive rotor shake; before they snowballed. Another example: A pulp and paper mill used wireless vibration sensors to monitor conveyor motors. They dodged a shutdown that could’ve cost $50,000 a day. Proconex clients see these gains all the time; smart monitoring, smarter outcomes.
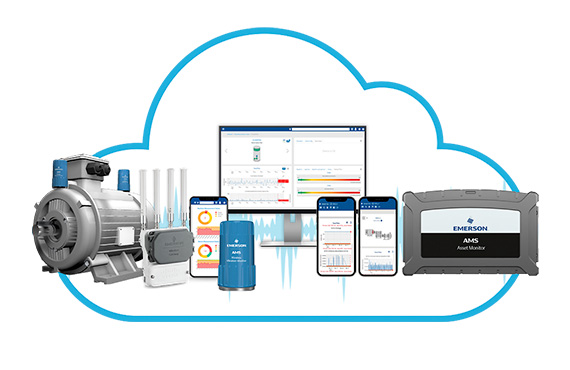
Applications That Thrive with Wireless Vibration Sensors
Industries we serve at Proconex lean on this tech daily. Here’s where it shines:
- Oil and Gas: Vibration wireless sensors track pumps and compressors in remote pipelines. No cables, no problem. Cross Company showcases this use: https://www.crossco.com/process-solutions/vibration-monitoring/.
- Chemical Manufacturing: Monitor reactors and mixers without invasive setups. A client caught bearing wear early, saving a week of downtime.
- Power Generation: Turbines and generators hum smoother with constant vibration checks. Efficiency gains hit 15 percent, per industry data.
- Water and Wastewater: Pumps stay online with wireless sensors flagging issues like cavitation; critical for uninterrupted service.
- Life Sciences: Sterile environments love the no-contact install. Precision keeps production rolling.
The market agrees. A Grand View Research report predicts wireless sensor adoption will climb 8 percent yearly through 2030. Why? They’re flexible, reliable, and cost-effective; exactly what modern operations need.
Boost Efficiency and Cut Costs
Efficiency isn’t a buzzword; it’s your edge. Wireless vibration sensors trim fat from your operation. Real-time alerts slash downtime by 30 percent, says Manufacturing.net. Predictive maintenance; driven by sensor data—cuts repair bills by 20–25 percent, per Maintenance Technology. Energy use drops too; optimized machines waste less power, saving 10–15 percent on bills.
Picture this: An oil refinery fitted wireless vibration sensors on centrifugal pumps. They caught a misalignment early, dodging a $75,000 repair and a day of lost output. Another win—a food processing plant tracked conveyor belts with these sensors, boosting throughput by 12 percent. Proconex brings that kind of ROI to your doorstep; less chaos, more control.
Why Wireless Beats Wired Everytime
Wired sensors have their place, but they’re dinosaurs next to wireless vibration sensors. Cables snag, corrode, and limit where you can monitor. Installation drags on, chewing up labor hours. Wireless? It’s a different story. Stick them on, sync them up, and you’re done. A Control Engineering study found wireless setups deploy 50 percent faster than wired ones. Plus, they reach spots; like high-up motors or remote tanks—wires can’t touch.
A steel mill swapped wired sensors for wireless on their rolling mills. Result? Maintenance dropped 35 percent, and they monitored twice as many assets. That’s not just savings; it’s a whole new way to run.
Why Proconex for Your Machine Health Monitoring System
Proconex has 75+ years of process control expertise; since 1948, we’ve been solving tough problems. We pair that legacy with cutting-edge tools like wireless vibration sensors from Emerson. Our team of 200+ pros serves industries like:
- Oil and gas
- Chemical manufacturing
- Power generation
- Water and wastewater
- Life sciences
We don’t just sell sensors; we build solutions. Need a machine health monitoring system for a refinery? We’ll spec it out. Tracking vibrations in a biotech lab? We’ve got the gear. Our partnership with Emerson ensures you get top-tier tech, tailored to your operation.
The Future of Machine Monitoring
This isn’t a fad; it’s the future. The IndustryWeek forecast sees predictive tech like wireless vibration sensors dominating by 2030. Why? Data rules. These sensors feed your team real-time stats; vibration spikes, frequency shifts, wear patterns. Pair them with analytics, and you’re not just monitoring; you’re mastering your machines.
A water treatment plant used wireless vibration sensors to predict pump failures a month out. They scheduled fixes during planned downtime, saving $30,000 in emergency repairs. That’s the power Proconex unlocks; foresight, not firefighting.
Take Control Today
Wireless vibration sensors turn machine health monitoring into a strategic advantage. They catch problems early, cut costs, and keep your operation humming. Ready to ditch downtime and boost efficiency? Proconex offers the tools and know-how to make it happen. Explore our wireless vibration sensor solutions at proconexdirect.com and see how we can power up your machine monitoring game.