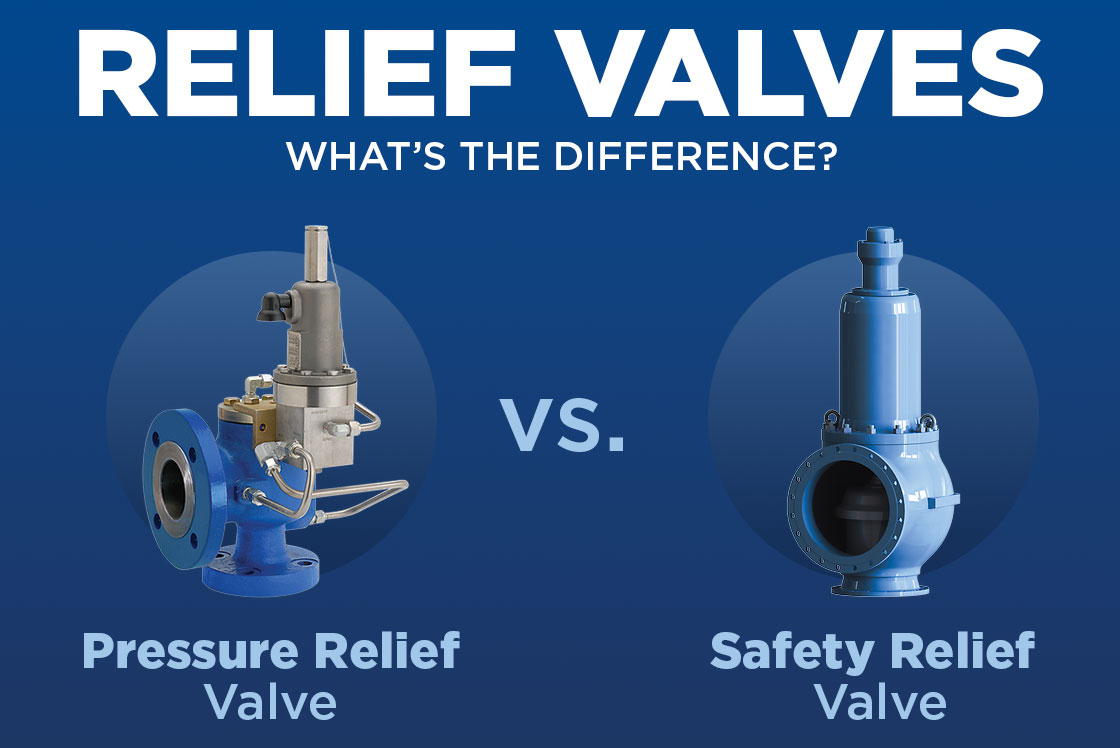
Relief valves are critical components that ensure the safety of your industrial system. These devices act as guardians in various facilities, including chemical processing plants and power generation stations, safeguarding both equipment and personnel from the hazards of excessive pressure.
Relief valves automatically regulate pressure in systems that handle pressurized fluids and gases. It’s kind of like when a tea kettle starts whistling. When pressure levels exceed predetermined limits, these valves open to release excess pressure, preventing potential equipment failures and hazards. In industrial settings, you'll primarily come across two types of relief valves:
Pressure Relief Valve (PRV): Designed for controlled pressure release in specific applications.
Safety Relief Valve (SRV): Built for quick response during emergencies.
Knowing the differences between these valve types is essential for: maintaining system integrity, ensuring workplace safety, complying with regulations, protecting valuable equipment, and optimizing operational efficiency.
This post will help you understand the distinctions between pressure relief valves and safety relief valves, empowering you to make informed decisions for your unique industrial requirements.
Understanding Relief Vales
Relief valves are important safety devices in pressurized systems. They act as automatic protectors against dangerous pressure buildup. When the pressure exceeds a certain limit, these mechanical devices automatically release fluid to prevent any harm to your equipment and personnel.
Primary Functions:
- Prevent system overpressure
- Maintain safe operating conditions
- Protect equipment integrity
- Safeguard personnel
Hazards of Inadequate Pressure Control:
- Catastrophic equipment failure
- Explosive decompressions
- Toxic material leaks
- System ruptures
- Personnel injuries
Relief valves come in different types to meet specific operational needs:
Common Types:
- Spring-loaded Valves: Quick-acting devices using mechanical force
- Pilot-operated Valves: Precise control for larger systems
- Balanced Bellows: Designed for back pressure resistance
- Rupture Disks: One-time use emergency pressure release
- Proportional Relief Valves: Gradual pressure release systems
Each type has its own advantages for different applications, whether it's simple pressure management or complex emergency situations. The choice of which type to use depends on factors such as system pressure, required response time, and operating environment.
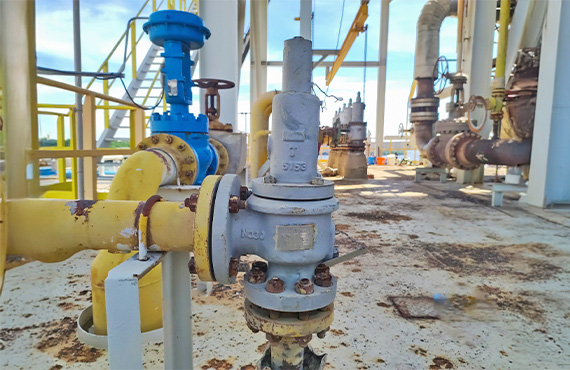
How Do Pressure Relief Valves Work?
The operation of a pressure relief valve is simple but crucial. When the pressure in the system exceeds a certain limit (set by the manufacturer), it puts pressure on the valve. This pressure overcomes the resistance of the spring, causing the valve disc to lift. As a result, excess pressure is released through the discharge outlet, bringing the system back to safe levels.
Key Components and Design Features
PRVs have specific features that make them effective:
- Spring-loaded mechanism: This allows for precise control of pressure.
- Adjustable pressure settings: The valve can be customized to open at different pressures as needed.
- Quick-response activation system: The valve opens rapidly when triggered by high pressure.
- Leak-tight sealing for normal operation: This ensures no pressure escapes during regular functioning.
- Corrosion-resistant materials: The valve is built to withstand harsh environments.
Common PRV Applications
You can find pressure relief valves in various industries and applications:
- Steam boilers and pressure vessels
- Industrial process equipment
- Oil and gas pipelines
- Chemical processing plants
- Pharmaceutical manufacturing
- HVAC systems
Importance of Proper Sizing
To ensure optimal performance, it's crucial to size your PRV correctly. Here's why:
- An undersized valve won't release pressure quickly enough, which could lead to dangerous situations.
- An oversized valve might cause instability in the system, affecting its overall efficiency.
Consider these factors when determining the right size for your valve: maximum flow rate requirements, operating temperature range, process fluid properties (such as viscosity or density), system pressure limitations, installation location constraints (such as available space)
Matching Discharge Capacity with Pressure Buildup Rate
The discharge capacity of your pressure relief valve must align with the potential rate at which pressure can build up in your system. This is critical for ensuring adequate protection during worst-case scenarios like equipment failures or unexpected changes in processes.
Importance of Regular Maintenance and Testing
To maintain the reliability of your PRVs, it's essential to schedule regular maintenance and testing activities. Here are some key aspects to focus on during inspections:
- Checking spring tension accuracy
- Verifying seat tightness (ensuring no leaks)
- Inspecting for corrosion or wear on components
- Ensuring proper alignment of all parts
- Confirming free movement of all movable components
Understanding Safety Relief Valves
Safety Relief Valves (SRVs) are essential devices used in pressurized systems to ensure safety. They provide protection against both high-pressure and low-pressure situations, making them versatile in their application.
Unlike standard pressure relief valves, SRVs have advanced features that allow them to respond quickly and handle various types of media (substances) flowing through them.
How Do Safety Relief Valves Work?
When the pressure in a system exceeds a certain limit (set point), the SRV activates to release excess pressure and prevent any potential damage. Here's a breakdown of how SRVs function:
- Pressure Detection: The valve constantly monitors the pressure in the system.
- Activation: Once the pressure surpasses the set point, the valve's disc lifts proportionally to the increase in pressure.
- Media Discharge: This lifting action allows for rapid release of excess media (gas or liquid) from the system, bringing it back within safe operating limits.
The quick response time of SRVs is crucial in preventing catastrophic failures and ensuring equipment integrity.
Industries That Depend on Safety Relief Valves
Several industries rely heavily on SRVs to maintain safety standards and protect their operations. Here are some key sectors where these valves play a vital role:
1. Oil and Gas Refineries
In oil and gas refineries, SRVs are used to safeguard distillation columns - critical equipment involved in separating different components of crude oil. By preventing overpressure situations during distillation processes, these valves help maintain product quality and prevent accidents.
2. Pharmaceutical Manufacturing
Pharmaceutical manufacturing facilities require stringent control over their processes to ensure sterile conditions. SRVs are employed to protect sterile process vessels from excessive pressure buildup, safeguarding the integrity of pharmaceutical products.
3. Power Generation Facilities
Steam systems are integral to power generation plants as they drive turbines for electricity production. SRVs secure these steam systems by relieving excess pressure when necessary, ensuring efficient operation and preventing equipment failures.
4. Chemical Processing Plants
Chemical reactions can be highly exothermic (releasing heat) or endothermic (absorbing heat). To maintain reactor safety during such reactions, chemical processing plants utilize SRVs that can quickly relieve pressure if it exceeds safe limits.
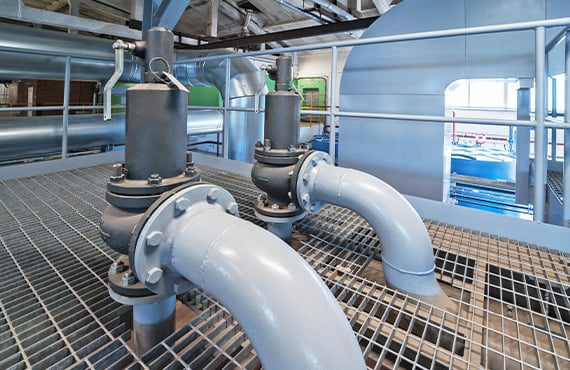
Applications Where Safety Relief Valves Prove Invaluable
SRVs find application in various high-stakes scenarios where maintaining proper pressure levels is critical:
- Steam Boiler Protection: Boilers generate steam under high pressures; thus, having an effective means of relieving excess pressure is essential to avoid explosive situations.
- Tank Farm Operations: Storage tanks containing liquids may experience thermal expansion due to temperature changes. SRVs help manage this expansion by allowing vapor or liquid release when required.
- Process Reactor Systems: Certain chemical processes involve exothermic reactions that produce heat rapidly. To prevent runaway reactions leading to accidents or equipment damage, SRVs are employed as safety devices.
- Cryogenic Storage: Cryogenic fluids (such as liquefied gases) require careful handling due to their low temperatures and potential phase transitions. SRVs ensure safe storage by relieving excess pressure during such transitions.
Key Differences Between Pressure Relief Valves and Safety Relief Valves
Understanding the distinct characteristics between Pressure Relief Valves (PRVs) and Safety Relief Valves (SRVs) helps you make informed decisions for your system requirements. Here are the key differentiating factors:
1. Design and Operation
- PRVs use a modulating action, opening gradually in proportion to pressure increase
- SRVs feature rapid opening "pop" action, releasing pressure quickly at set points
- PRVs typically incorporate pilot-operated mechanisms for precise control
- SRVs often use direct spring-loaded designs for immediate response
2. Response Characteristics
PRVs:
- Open at 3-5% above set pressure
- Close at 2-4% below set pressure
- Gradual pressure release
SRVs:
- Pop open at exact set pressure
- Feature 10-20% blowdown
- Rapid pressure discharge
3. Industry Applications
PRVs excel in:
- Process industries
- Hydraulic systems
- Continuous flow operations
SRVs are preferred for:
- Steam boilers
- Compressed air systems
- Emergency scenarios
4. Regulatory Standards
- ASME Section VIII governs PRV installations
- ASME Section I regulates SRV requirements for power boilers
- API RP 520/521 provides sizing guidelines for both valve types
5. Performance Parameters
- PRVs maintain steady system pressure through controlled release
- SRVs prioritize rapid pressure reduction in emergency situations
- PRVs handle normal process variations
- SRVs focus on preventing catastrophic equipment failure
These distinctions guide valve selection based on your specific application requirements, safety protocols, and industry regulations.
Key Takeaways
Relief valves are essential safety devices in industrial operations. They help protect systems from excessive pressure and ensure the safety of equipment and personnel. There are two main types of relief valves: pressure relief valves and safety relief valves, each serving a specific purpose in system protection.
The choice between these two valve types can have a significant impact on your facility's safety and operational efficiency. Pressure relief valves are designed to gradually release pressure, making them suitable for steady-state operations. On the other hand, safety relief valves provide quick response capabilities, which are crucial during emergencies or sudden pressure increases.
When selecting the right valve for your system, it's important to consider its specific requirements. Factors such as operating conditions, media type, and industry regulations should all be considered. By thoroughly assessing these factors, you can develop an effective pressure management strategy that safeguards both equipment and personnel.
To maintain optimal safety standards as your operational requirements evolve, it's essential to regularly evaluate your pressure relief needs. This proactive approach to pressure management not only strengthens your safety protocols but also supports long-term operational success.
Explore Our Valve Repair Solutions!
Our Comprehensive Services Include:
- Complete valve inspection and diagnostics
- Precision calibration and testing
- Component replacement and repairs
- Performance certification
- Emergency repair services
We understand the critical nature of your operations. Our certified technicians use state-of-the-art equipment to ensure your valves meet industry standards and specifications.
Why Choose Our Valve Install and Repair Services?
- 24/7 Emergency Support: Quick response times when you need immediate assistance
- Certified Expertise: Our team holds relevant industry certifications and 75+ years of being in the industrial valve space
- Quality Assurance: All repairs meet or exceed manufacturer specifications
- Detailed Documentation: Complete service reports and certification records
Ready to ensure your valve systems operate at their best?
Schedule your valve inspection now and protect your critical systems with professional maintenance and repair services.