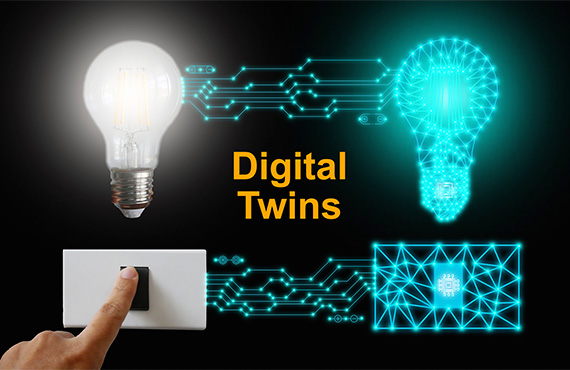
Digital twin simulation software is a groundbreaking technology that is transforming industrial operations. It enables you to create an exact digital replica of your industrial equipment that reflects its physical counterpart in real-time.
Digital twin simulation technology utilizes cutting-edge sensors and data analysis techniques to generate virtual replicas of tangible assets, capturing every aspect of their operation. With these digital versions, you can:
- Monitor equipment performance in real-time
- Predict maintenance needs before failures occur
- Test modifications virtually before implementing them
- Optimize operations without disrupting production
As industries shift towards smarter and more efficient operations, it's crucial to understand digital twin technology to remain competitive. At Proconex we have witnessed firsthand how digital twin software solutions are revolutionizing processes in various sectors including Life Sciences, Chemical, Power, and beyond.
With over 75 years of industry experience, we help businesses use this powerful technology to:
- Improve their operational efficiency
- Reduce costs
- Foster innovation
Whether you are in chemical manufacturing, oil and gas, or food and beverage, digital twin simulation software has the potential to unlock new opportunities for operational excellence.
Understanding Digital Twin Technology
Think of digital twin software as a mirror that shows you a living, breathing copy of your real-world equipment, processes, or systems. Just like how your reflection moves when you move, these virtual doubles match their physical twins down to the smallest detail - from how they work to how well they perform. It's kind of like having a practice playground where companies can test out new ideas and make improvements without touching the actual machinery or disrupting their day-to-day operations.
The Origin of Digital Twins
Back in '91, NASA faced quite a challenge - they needed to figure out how to keep their spacecraft running smoothly when they couldn't exactly walk up and fix them in space. That's when they came up with this brilliant idea of creating virtual copies of their systems. Think of it like having a practice dummy for a doctor, but way more high-tech! It wasn't until about a decade later that a brilliant man by the name of Dr. Michael Grieves took this idea and ran with it at the University of Michigan. In 2002, he basically wrote the rulebook for how we could use these virtual twins in all sorts of ways - not just for spaceships. He really helped everyone understand how this cool tech could work in the real world.
The Evolution of Digital Twin Technology
The evolution of digital twin software spans three distinct generations:
- First Generation (1991-2002): Basic digital representations focused on geometric properties
- Second Generation (2002-2014): Integration of behavioral and performance data
- Third Generation (2014-Present): Advanced AI and IoT capabilities enabling predictive analytics
NASA's Role in Pioneering Digital Twins
You know what's really cool? NASA kicked off this whole digital twin thing back in the Apollo days. They had this clever setup where they built exact copies of their spacecraft systems right here on Earth. That way, when their astronauts ran into problems up in space, the engineers could figure out solutions using these Earth-bound duplicates. Pretty smart, right? Looking back, it's amazing how this creative problem-solving approach by NASA ended up sparking a revolution that's now helping all kinds of different industries work better.
How Digital Twin Software Works Today
Today's digital twin simulation software incorporates advanced technologies:
- Real-time data streaming
- Machine learning algorithms
- IoT sensor integration
- Cloud computing capabilities
- Advanced visualization tools
When all these pieces of technology join forces, they paint a vivid, living picture of real-world equipment and systems. This helps companies run smoother, spot problems before they happen, and come up with creative new ways to improve their day-to-day operations.
How Does Digital Twin Software Work?
Digital twin simulation technology operates through a sophisticated network of sensors and data processing systems. Here's a detailed look at the core mechanisms:
1. Data Collection Through IoT Sensors
- Industrial IoT sensors capture real-time performance metrics
- Multiple data points track temperature, pressure, vibration, and speed
- Advanced sensors monitor environmental conditions and operational parameters
- Continuous data streams enable instant detection of anomalies
2. Creating the Digital Counterpart
- Raw sensor data undergoes processing through specialized algorithms
- AI-powered systems transform data into actionable insights
- Real-time updates sync physical asset changes with digital model
- Cloud computing platforms store and process vast amounts of operational data
3. Simulation and Machine Learning Integration
- Digital models run thousands of simulations to predict outcomes
- Machine learning algorithms identify patterns and trends
- Predictive analytics forecast potential equipment failures
- Virtual testing environments evaluate different scenarios without risk
The integration of these components creates a dynamic system where physical assets communicate directly with their digital counterparts through digital twin software. Engineers can manipulate virtual models to test modifications, while machine learning algorithms continuously improve predictions based on accumulated data. This real-time synchronization enables:
- Rapid response to operational changes
- Accurate performance predictions
- Risk-free testing of new configurations
- Data-driven decision making
- Enhanced operational efficiency
The use of sensor technology, real-time updates, and advanced analytics turns raw data into valuable insights that lead to operational improvements in industrial processes.
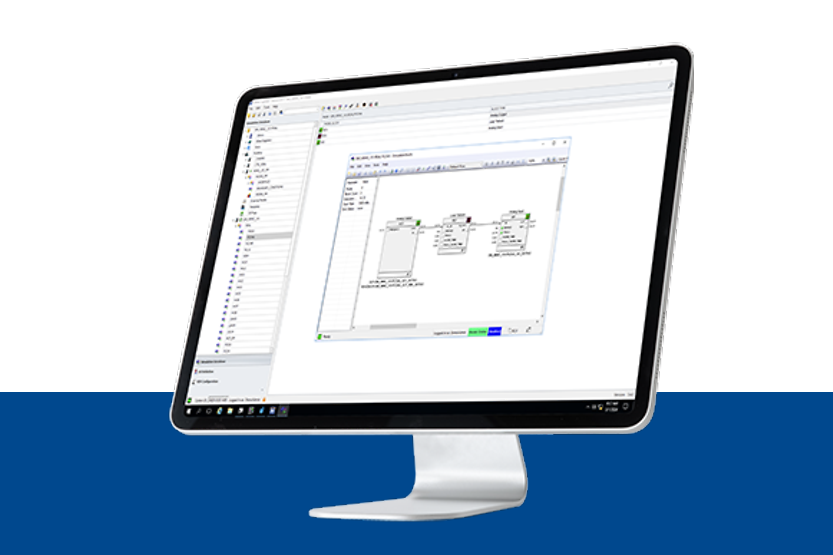
Different Types of Digital Twins and Their Applications
Digital twin technology adapts to diverse industrial needs through four distinct categories, each serving unique operational purposes.
1. Component Twins
Component twins replicate individual parts or components within a larger system. These digital replicas track:
- Wear and tear patterns
- Performance metrics
- Maintenance requirements
- Failure predictions
Real-world application: Take the aviation industry, for example - engineers are using digital replicas to keep a close eye on how jet engine turbine blades are holding up. By carefully watching how these critical components perform in real-time, maintenance teams can spot potential issues early and schedule repairs before anything goes wrong. It's like having a crystal ball that helps prevent costly breakdowns and keeps planes flying safely.
2. Asset Twins
Asset twins represent complete machines or equipment units, providing comprehensive insights into:
- Operational efficiency
- Energy consumption
- Performance optimization
- Maintenance scheduling
Real-world application: Imagine a busy factory where managers are using digital technology to ensure everything operates efficiently. They've developed virtual versions of their assembly lines that function as digital observers, always monitoring the actual machines. These digital replicas assist the team in identifying possible issues before they occur and discovering innovative methods to enhance production. It's like having a protective figure for each machine, ensuring everything functions seamlessly and reducing expensive equipment failures.
3. System Twins
System twins model interconnected networks of assets, enabling:
- System-wide performance analysis
- Resource allocation optimization
- Bottleneck identification
- Emergency response planning
Real-world application: In today's modern urban landscapes, city planners and managers have embraced an innovative approach by creating virtual replicas of their infrastructure. These digital models help them keep our cities running smoothly - from making sure traffic moves efficiently through busy streets, to ensuring the lights stay on in every neighborhood, and getting ambulances to emergencies as quickly as possible. Think of it as having a detailed, living map that helps city officials make better decisions about how to keep everything working together harmoniously for the benefit of all residents.
4. Process Twins
Process twins simulate entire operational workflows, focusing on:
- Production efficiency
- Quality control
- Resource utilization
- Supply chain optimization
Real-world application: In the fast-paced world of chemical manufacturing, plant operators have found a game-changing ally in digital process twins.
Imagine having a virtual copy of the entire production line, where engineers can make precise adjustments to their chemical reactions as they happen. These advanced digital tools empower workers to ensure that each batch meets strict quality standards while keeping operations running smoothly. It's as if they have a special device that gives them a clear view of every part of the production process, allowing them to fix problems before they occur and maintain the high quality of their products.
Each type of digital twin serves specific industries and applications:
- The oil and gas sector relies on asset twins for equipment monitoring.
- Pharmaceutical manufacturers use process twins for quality control.
- The automotive industry combines component and system twins to enhance vehicle design and production.
- These digital twin categories work together in many applications. For example, a manufacturing facility may use:
- Component twins for critical machinery parts
- Asset twins for entire production lines
- Process twins to optimize the complete manufacturing workflow
How Is Digital Twin Technology Transforming Industrial Operations
Digital twin technology significantly reduces costs in industrial sectors by enabling accurate, data-driven operations management. In the oil and gas industry, digital twins have been able to lower operational expenses by 10-30% through:
- Reduced downtime - Real-time monitoring detects potential equipment failures before they occur
- Optimized maintenance - Condition-based scheduling replaces time-based maintenance
- Enhanced safety - Virtual testing of dangerous scenarios without risking personnel or equipment
- Lower energy consumption - Optimized operations reduce power usage by 15-25%
Manufacturing facilities implementing digital twins report significant improvements in operational efficiency:
- 25% reduction in maintenance costs
- 20% decrease in asset downtime
- 40% improvement in maintenance staff productivity
- 15-30% reduction in capital expenditure
The technology enables precise design improvements through virtual testing and validation.
Engineers can:
- Test multiple design iterations without physical prototypes
- Identify potential failures before production
- Optimize product performance in simulated environments
- Reduce time-to-market for new products
Digital twins transform maintenance scheduling by providing:
- Real-time asset health monitoring
- Predictive maintenance alerts
- Performance optimization recommendations
- Resource allocation guidance
These capabilities allow organizations to move from reactive to proactive maintenance strategies. Companies can plan maintenance activities during scheduled downtimes, minimizing unexpected failures and maximizing asset availability.
Integrating digital twin simulation software with current industrial systems allows for a smooth exchange of operational data. This connection makes it possible to automate decision-making and quickly adapt to changing circumstances, leading to more efficient production and lower operating costs.
Beyond Cost Efficiency: The Wider Advantages Offered by Digital Twins
Digital twin technology extends far beyond cost savings, transforming how businesses interact with customers and manage their assets.
Enhanced Customer Experience
- Real-time product performance monitoring enables rapid response to customer needs
- Customization capabilities allow products to be tailored to specific customer requirements
- Virtual product demonstrations help customers understand features before purchase
- Remote troubleshooting reduces downtime and service wait times
Advanced Predictive Maintenance
- Early detection of potential equipment failures through pattern recognition
- AI-powered analysis of performance data identifies maintenance needs before breakdowns occur
- Scheduled maintenance based on actual equipment condition rather than fixed intervals
- Reduced emergency repairs through proactive intervention
Data-Driven Decision Making
- Historical performance data guides product improvements
- Detailed usage patterns inform future design iterations
- Real-world testing scenarios in virtual environments
- Risk assessment and mitigation strategies based on digital simulations
The integration of digital twins creates a dynamic feedback loop between manufacturers and end-users. This continuous exchange of data enables companies to refine their products while delivering superior service. Companies can now anticipate customer needs and address potential issues before they impact operations, marking a shift from reactive to proactive business models.
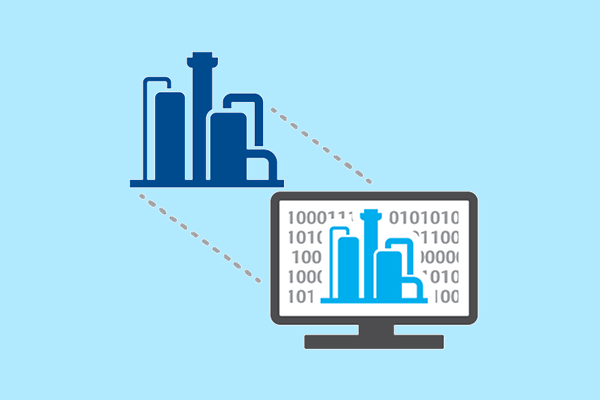
Future Trends Shaping Digital Twin Technology
The digital twin simulation software market is experiencing explosive growth, with projections reaching USD 73.5 billion by 2027. This remarkable expansion is due to the increasing use of digital technology in industries and the growing need for predictive maintenance solutions in various sectors.
Key Growth Drivers
Key growth drivers include:
- 5G Technology Integration: Enhanced connectivity enables real-time data processing and faster digital twin responses
- AI and Machine Learning Advancement: Smarter algorithms improve prediction accuracy and autonomous decision-making
- IoT Sensor Evolution: More sophisticated sensors capture detailed operational data
- Cloud Computing Scalability: Expanded storage and processing capabilities support complex simulations
Integration of Physical Digital Assets
The integration of physical and digital assets is reaching new heights through:
- Enhanced Reality Integration: AR/VR technologies enabling immersive digital twin interactions
- Cross-Industry Collaboration: Manufacturing facilities sharing digital twin insights to optimize supply chains
- Blockchain Implementation: Secure data sharing and verification between connected systems
- Edge Computing: Faster processing of critical data at the source
Innovative Applications Across Industries
Industries are witnessing innovative applications:
- Smart cities using digital twins to optimize traffic flow and energy consumption
- Healthcare facilities creating patient-specific treatment simulations
- Aerospace companies developing digital twin-powered flight simulators
- Automotive manufacturers streamlining production through virtual testing
The rise of "Digital Thread" technology connects different stages of product lifecycle management, creating seamless data flow between design, manufacturing, and maintenance phases. This integration enables real-time optimization and creates new opportunities for innovation across industrial operations.
Final Thought: Proconex's Leadership in the Digital Twin Revolution
The way digital twin software has shaken up how industries work is remarkable - it's like we've entered a whole new chapter in running businesses smarter. You know how your phone's GPS creates a real-time map of where you are? Well, imagine that but for entire factories and machines. Companies are using this tech to make better calls based on actual data rather than gut feelings, and it's really paying off.
It's fascinating how these virtual copies of real-world equipment and processes are helping businesses work more efficiently - from keeping machines running smoothly to coming up with creative solutions to old problems. It's kind of like having a crystal ball that lets you see how changes might play out before you make them in real life.
With over 75 years of industry experience, Proconex offers:
- State-of-the-art process automation control and safety systems
- Advanced valves, actuators, and regulators
- Comprehensive digital twin software
- Expert implementation and support services
- Our dedicated team of over 200 professionals caters to various industries:
Your journey towards digital transformation begins with selecting the right partner. Proconex combines extensive industry expertise with Emerson's cutting-edge solutions to empower you in leveraging digital twin technology.
Get in touch with our team to discover how our digital twin solutions can enhance your processes and promote sustainable growth. Together, let's construct your digital future.